Industrial Revolution
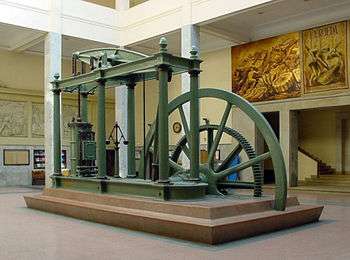
The Industrial Revolution was the transition to new manufacturing processes in the period from about 1760 to sometime between 1820 and 1840. This transition included going from hand production methods to machines, new chemical manufacturing and iron production processes, improved efficiency of water power, the increasing use of steam power, the development of machine tools and the rise of the factory system. Textiles were the dominant industry of the Industrial Revolution in terms of employment, value of output and capital invested; the textile industry was also the first to use modern production methods.[1] The Industrial Revolution began in Great Britain and most of the important technological innovations were British. The social, economic and political changes in the previous centuries in Great Britain contributed. Whereas absolutism stayed the normal form of power execution through most parts of Europe, institutions ensured property rights and political safety to the people in the UK after the Glorious Revolution of 1688. A change in marrying patterns to getting married later made people able to accumulate more human capital during their youth, thereby encouraging economic development.[2]
The Industrial Revolution marks a major turning point in history; almost every aspect of daily life was influenced in some way. In particular, average income and population began to exhibit unprecedented sustained growth. Some economists say that the major impact of the Industrial Revolution was that the standard of living for the general population began to increase consistently for the first time in history, although others have said that it did not begin to meaningfully improve until the late 19th and 20th centuries.[3][4][5] At approximately the same time the Industrial Revolution was occurring, Britain was undergoing an agricultural revolution, which also helped to improve living standards and provided surplus labour available for industry.
Mechanised textile production spread from Great Britain to continental Europe in the early 19th century, with important centres of textiles, iron and coal emerging in Belgium, and later in France. Since then industrialisation has spread throughout much of the world.[1] The precise start and end of the Industrial Revolution is still debated among historians, as is the pace of economic and social changes.[6][7][8][9] GDP per capita was broadly stable before the Industrial Revolution and the emergence of the modern capitalist economy,[10] while the Industrial Revolution began an era of per-capita economic growth in capitalist economies.[11] Economic historians are in agreement that the onset of the Industrial Revolution is the most important event in the history of humanity since the domestication of animals and plants.[12]
The First Industrial Revolution evolved into the Second Industrial Revolution in the transition years between 1840 and 1870, when technological and economic progress continued with the increasing adoption of steam transport (steam-powered railways, boats and ships), the large-scale manufacture of machine tools and the increasing use of machinery in steam-powered factories.[13][14][15]
Etymology
The earliest recorded use of the term "Industrial Revolution" seems to have been in a letter from 6 July 1799 written by French envoy Louis-Guillaume Otto, announcing that France had entered the race to industrialise.[16] In his 1976 book Keywords: A Vocabulary of Culture and Society, Raymond Williams states in the entry for "Industry": "The idea of a new social order based on major industrial change was clear in Southey and Owen, between 1811 and 1818, and was implicit as early as Blake in the early 1790s and Wordsworth at the turn of the [19th] century." The term Industrial Revolution applied to technological change was becoming more common by the late 1830s, as in Jérôme-Adolphe Blanqui's description in 1837 of la révolution industrielle.[17] Friedrich Engels in The Condition of the Working Class in England in 1844 spoke of "an industrial revolution, a revolution which at the same time changed the whole of civil society". However, although Engels wrote in the 1840s, his book was not translated into English until the late 1800s, and his expression did not enter everyday language until then. Credit for popularising the term may be given to Arnold Toynbee, whose 1881 lectures gave a detailed account of the term.[18]
Some historians, such as John Clapham and Nicholas Crafts, have argued that the economic and social changes occurred gradually and the term revolution is a misnomer. This is still a subject of debate among some historians.
Important technological developments
The commencement of the Industrial Revolution is closely linked to a small number of innovations,[19] beginning in the second half of the 18th century. By the 1830s the following gains had been made in important technologies:
- Textiles – mechanised cotton spinning powered by steam or water greatly increased the output of a worker. The power loom increased the output of a worker by a factor of over 40.[20] The cotton gin increased productivity of removing seed from cotton by a factor of 50.[14] Large gains in productivity also occurred in spinning and weaving of wool and linen, but they were not as great as in cotton.[21]
- Steam power – the efficiency of steam engines increased so that they used between one-fifth and one-tenth as much fuel. The adaptation of stationary steam engines to rotary motion made them suitable for industrial uses.[22] The high pressure engine had a high power to weight ratio, making it suitable for transportation.[23] Steam power underwent a rapid expansion after 1800.
- Iron making – the substitution of coke for charcoal greatly lowered the fuel cost for pig iron and wrought iron production.[24] Using coke also allowed larger blast furnaces,[25][26] resulting in economies of scale. The cast iron blowing cylinder was first used in 1760. It was later improved by making it double acting, which allowed higher furnace temperatures. The puddling process produced a structural grade iron at a lower cost than the finery forge.[27] The rolling mill was fifteen times faster than hammering wrought iron. Hot blast (1828) greatly increased fuel efficiency in iron production in the following decades.
Textile manufacture
In the late 17th and early 18th centuries the British government passed a series of Calico Acts in order to protect the domestic woollen industry from the increasing amounts of cotton fabric imported from its competitors in India.[22][28]
The demand for heavier fabric was met by a domestic industry based around Lancashire that produced fustian, a cloth with flax warp and cotton weft. Flax was used for the warp because wheel-spun cotton did not have sufficient strength, but the resulting blend was not as soft as 100% cotton and was more difficult to sew.[28]
On the eve of the Industrial Revolution, spinning and weaving were done in households, for domestic consumption and as a cottage industry under the putting-out system. Occasionally the work was done in the workshop of a master weaver. Under the putting-out system, home-based workers produced under contract to merchant sellers, who often supplied the raw materials. In the off season the women, typically farmers' wives, did the spinning and the men did the weaving. Using the spinning wheel, it took anywhere from four to eight spinners to supply one hand loom weaver.[21][28][29]:823 The flying shuttle patented in 1733 by John Kay, with a number of subsequent improvements including an important one in 1747, doubled the output of a weaver, worsening the imbalance between spinning and weaving. It became widely used around Lancashire after 1760 when John's son, Robert, invented the drop box.[29]:821–22
Lewis Paul patented the roller spinning frame and the flyer-and-bobbin system for drawing wool to a more even thickness. The technology was developed with the help of John Wyatt of Birmingham. Paul and Wyatt opened a mill in Birmingham which used their new rolling machine powered by a donkey. In 1743 a factory opened in Northampton with 50 spindles on each of five of Paul and Wyatt's machines. This operated until about 1764. A similar mill was built by Daniel Bourn in Leominster, but this burnt down. Both Lewis Paul and Daniel Bourn patented carding machines in 1748. Based on two sets of rollers that travelled at different speeds, it was later used in the first cotton spinning mill. Lewis's invention was later developed and improved by Richard Arkwright in his water frame and Samuel Crompton in his spinning mule.

In 1764 in the village of Stanhill, Lancashire, James Hargreaves invented the spinning jenny, which he patented in 1770. It was the first practical spinning frame with multiple spindles.[30] The jenny worked in a similar manner to the spinning wheel, by first clamping down on the fibres, then by drawing them out, followed by twisting.[31] It was a simple, wooden framed machine that only cost about £6 for a 40-spindle model in 1792,[32] and was used mainly by home spinners. The jenny produced a lightly twisted yarn only suitable for weft, not warp.[29]:825–27
The spinning frame or water frame was developed by Richard Arkwright who, along with two partners, patented it in 1769. The design was partly based on a spinning machine built for Thomas High by clockmaker John Kay, who was hired by Arkwright.[29]:827–30 For each spindle, the water frame used a series of four pairs of rollers, each operating at a successively higher rotating speed, to draw out the fibre, which was then twisted by the spindle. The roller spacing was slightly longer than the fibre length. Too close a spacing caused the fibres to break while too distant a spacing caused uneven thread. The top rollers were leather-covered and loading on the rollers was applied by a weight. The weights kept the twist from backing up before the rollers. The bottom rollers were wood and metal, with fluting along the length. The water frame was able to produce a hard, medium count thread suitable for warp, finally allowing 100% cotton cloth to be made in Britain. A horse powered the first factory to use the spinning frame. Arkwright and his partners used water power at a factory in Cromford, Derbyshire in 1771, giving the invention its name.

Samuel Crompton's Spinning Mule, introduced in 1779, was a combination of the spinning jenny and the water frame in which the spindles were placed on a carriage, which went through an operational sequence during which the rollers stopped while the carriage moved away from the drawing roller to finish drawing out the fibres as the spindles started rotating.[29]:832 Crompton's mule was able to produce finer thread than hand spinning and at a lower cost. Mule spun thread was of suitable strength to be used as warp, and finally allowed Britain to produce good quality calico cloth.[29]:832
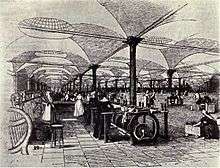
Realising that the expiration of the Arkwright patent would greatly increase the supply of spun cotton and lead to a shortage of weavers, Edmund Cartwright developed a vertical power loom which he patented in 1785. In 1776 he patented a two-man operated loom which was more conventional.[29]:834 Cartwright built two factories; the first burned down and the second was sabotaged by his workers. Cartwright's loom design had several flaws, the most serious being thread breakage. Samuel Horrocks patented a fairly successful loom in 1813. Horock's loom was improved by Richard Roberts in 1822 and these were produced in large numbers by Roberts, Hill & Co.[33]
The demand for cotton presented an opportunity to planters in the Southern United States, who thought upland cotton would be a profitable crop if a better way could be found to remove the seed. Eli Whitney responded to the challenge by inventing the inexpensive cotton gin. With a cotton gin a man could remove seed from as much upland cotton in one day as would have previously taken a woman working two months to process at one pound per day.[14]
Other inventors increased the efficiency of the individual steps of spinning (carding, twisting and spinning, and rolling) so that the supply of yarn increased greatly. This in turn fed a weaving industry that advanced with improvements to shuttles and the loom or 'frame'. The output of an individual labourer increased dramatically, with the effect that the new machines threatened the bargaining power of the labourers, and early innovators were attacked and their inventions destroyed.[34]
These advances were capitalised on by entrepreneurs, of whom the best known is Richard Arkwright. He is credited with a list of inventions, but these were actually developed by such people as Thomas Highs and John Kay; Arkwright nurtured the inventors, patented the ideas, financed the initiatives, and protected the machines. He created the cotton mill which brought the production processes together in a factory, and he developed the use of power—first horse power and then water power—which made cotton manufacture a mechanised industry. Before long steam power was applied to drive textile machinery. Manchester acquired the nickname Cottonopolis during the early 19th century owing to its sprawl of textile factories.[35]
Metallurgy


A major change in the metal industries during the era of the Industrial Revolution was the replacement of wood and other bio-fuels with coal. For a given amount of heat, coal required much less labour to mine than cutting wood and converting it to charcoal,[36] and coal was more abundant than wood.[21]
Use of coal in smelting started somewhat before the Industrial Revolution, based on innovations by Sir Clement Clerke and others from 1678, using coal reverberatory furnaces known as cupolas. These were operated by the flames playing on the ore and charcoal or coke mixture, reducing the oxide to metal. This has the advantage that impurities (such as sulphur ash) in the coal do not migrate into the metal. This technology was applied to lead from 1678 and to copper from 1687. It was also applied to iron foundry work in the 1690s, but in this case the reverberatory furnace was known as an air furnace. (The foundry cupola is a different (and later) innovation.)
This was followed by Abraham Darby, who made great strides using coke to fuel his blast furnaces at Coalbrookdale in 1709. However, the coke pig iron he made was used mostly for the production of cast iron goods, such as pots and kettles. He had the advantage over his rivals in that his pots, cast by his patented process, were thinner and cheaper than theirs. Coke pig iron was hardly used to produce wrought iron in forges until the mid-1750s, when his son Abraham Darby II built Horsehay and Ketley furnaces (not far from Coalbrookdale). By then, coke pig iron was cheaper than charcoal pig iron. Since cast iron was becoming cheaper and more plentiful, it began being a structural material following the building of the innovative Iron Bridge in 1778 by Abraham Darby III.
Wrought iron for smiths to forge into consumer goods was still made in finery forges, as it long had been. However, new processes were adopted in the ensuing years. The first is referred to today as potting and stamping, but this was superseded by Henry Cort's puddling process. Cort developed two significant iron manufacturing processes: rolling in 1783 and puddling in 1784.[27] Rolling replaced hammering for consolidating wrought iron and expelling some of the dross. Rolling was 15 times faster than hammering with a trip hammer. Roller mills were first used for making sheets, but also were developed for rolling structural shapes such as angles and rails.
Puddling produced a structural grade iron at a relatively low cost. Puddling was a means of decarburizing pig iron by slow oxidation, with iron ore as the oxygen source, as the iron was manually stirred using a long rod. The decarburized iron, having a higher melting point than cast iron, was raked into globs by the puddler. When the glob was large enough the puddler would remove it. Puddling was backbreaking and extremely hot work. Few puddlers lived to be 40.[37] Puddling was done in a reverberatory furnace, allowing coal or coke to be used as fuel. The puddling process continued to be used until the late 19th century when iron was being displaced by steel. Because puddling required human skill in sensing the iron globs, it was never successfully mechanised.
Up to that time, British iron manufacturers had used considerable amounts of imported iron to supplement native supplies. This came principally from Sweden from the mid-17th century and later also from Russia from the end of the 1720s. However, from 1785, imports decreased because of the new iron making technology, and Britain became an exporter of bar iron as well as manufactured wrought iron consumer goods.
Hot blast, patented by James Beaumont Neilson in 1828, was the most important development of the 19th century for saving energy in making pig iron. By using waste exhaust heat to preheat combustion air, the amount of fuel to make a unit of pig iron was reduced at first by between one-third using coal or two-thirds using coke;[38] however, the efficiency gains continued as the technology improved.[39] Hot blast also raised the operating temperature of furnaces, increasing their capacity. Using less coal or coke meant introducing fewer impurities into the pig iron. This meant that lower quality coal or anthracite could be used in areas where coking coal was unavailable or too expensive;[40] however, by the end of the 19th century transportation costs fell considerably.
Two decades before the Industrial Revolution an improvement was made in the production of steel, which was an expensive commodity and used only where iron would not do, such as for cutting edge tools and for springs. Benjamin Huntsman developed his crucible steel technique in the 1740s. The raw material for this was blister steel, made by the cementation process.
The supply of cheaper iron and steel aided a number of industries, such as those making nails, hinges, wire and other hardware items. The development of machine tools allowed better working of iron, causing it to be increasingly used in the rapidly growing machinery and engine industries.
Steam power
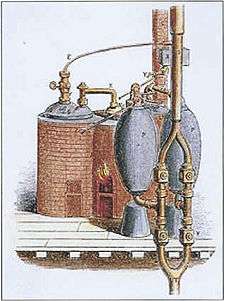
The development of the stationary steam engine was an important element of the Industrial Revolution; however, during the early period of the Industrial Revolution, the majority of industrial power was supplied by water and wind. In Britain by 1800 an estimated 10,000 horsepower was being supplied by steam. By 1815 steam power had grown to 210,000 hp.[41] Small industrial power requirements continued to be provided by animal and human muscle until widespread electrification in the early 20th century. These included crank, treadle powered and horse-powered workshop and light industrial machinery.[42]
The first commercially successful industrial use of steam power was due to Thomas Savery in 1698. He constructed and patented in London a low-lift combined vacuum and pressure water pump, that generated about one horsepower (hp) and was used in numerous water works and in a few mines (hence its "brand name", The Miner's Friend). Savery's pump was economical in small horsepower ranges, but was prone to boiler explosions in larger sizes. Savery pumps continued to be produced until the late 18th century.
The first successful piston steam engine was introduced by Thomas Newcomen before 1712. A number of Newcomen engines were successfully put to use in Britain for draining hitherto unworkable deep mines, with the engine on the surface; these were large machines, requiring a lot of capital to build, and produced about 5 hp (3.7 kW). They were extremely inefficient by modern standards, but when located where coal was cheap at pit heads, opened up a great expansion in coal mining by allowing mines to go deeper. Despite their disadvantages, Newcomen engines were reliable and easy to maintain and continued to be used in the coalfields until the early decades of the 19th century. By 1729, when Newcomen died, his engines had spread (first) to Hungary in 1722, Germany, Austria, and Sweden. A total of 110 are known to have been built by 1733 when the joint patent expired, of which 14 were abroad. In the 1770s the engineer John Smeaton built some very large examples and introduced a number of improvements. A total of 1,454 engines had been built by 1800.[43]

A fundamental change in working principles was brought about by Scotsman James Watt. In close collaboration with Englishman Matthew Boulton, he had succeeded by 1778 in perfecting his steam engine, which incorporated a series of radical improvements, notably the closing off of the upper part of the cylinder thereby making the low pressure steam drive the top of the piston instead of the atmosphere, use of a steam jacket and the celebrated separate steam condenser chamber. The separate condenser did away with the cooling water that had been injected directly into the cylinder, which cooled the cylinder and wasted steam. Likewise, the steam jacket kept steam from condensing in the cylinder, also improving efficiency. These improvements increased engine efficiency so that Boulton & Watts engines used only 20–25% as much coal per horsepower-hour as Newcomen's. Boulton and Watt opened the Soho Foundry, for the manufacture of such engines, in 1795.
By 1783 the Watt steam engine had been fully developed into a double-acting rotative type, which meant that it could be used to directly drive the rotary machinery of a factory or mill. Both of Watt's basic engine types were commercially very successful, and by 1800, the firm Boulton & Watt had constructed 496 engines, with 164 driving reciprocating pumps, 24 serving blast furnaces, and 308 powering mill machinery; most of the engines generated from 5 to 10 hp (7.5 kW).
The development of machine tools, such as the engine lathe, planing, milling and shaping machines powered by these engines, enabled all the metal parts of the engines to be easily and accurately cut and in turn made it possible to build larger and more powerful engines.
Until about 1800 the most common pattern of steam engine was the beam engine, built as an integral part of a stone or brick engine-house, but soon various patterns of self-contained rotative engines (readily removable, but not on wheels) were developed, such as the table engine. Around the start of the 19th century, the Cornish engineer Richard Trevithick, and the American, Oliver Evans began to construct higher pressure non-condensing steam engines, exhausting against the atmosphere. High pressure yielded an engine and boiler compact enough to be used on mobile road and rail locomotives and steam boats.
Machine tools
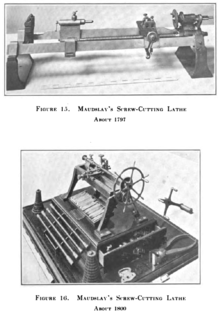
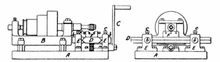
The Industrial Revolution created a demand for metal parts used in machinery. This led to the development of several machine tools for cutting metal parts. They have their origins in the tools developed in the 18th century by makers of clocks and watches and scientific instrument makers to enable them to batch-produce small mechanisms.
Before the advent of machine tools, metal was worked manually using the basic hand tools of hammers, files, scrapers, saws and chisels. Consequently, the use of metal was kept to a minimum. Wooden components had the disadvantage of changing dimensions with temperature and humidity, and the various joints tended to rack (work loose) over time. As the Industrial Revolution progressed, machines with metal parts and frames became more common. Hand methods of production were very laborious and costly and precision was difficult to achieve. Pre-industrial machinery was built by various craftsmen—millwrights built water and wind mills, carpenters made wooden framing, and smiths and turners made metal parts.
The first large machine tool was the cylinder boring machine used for boring the large-diameter cylinders on early steam engines. The planing machine, the milling machine and the shaping machine were developed in the early decades of the 19th century. Although the milling machine was invented at this time, it was not developed as a serious workshop tool until somewhat later in the 19th century.
Henry Maudslay, who trained a school of machine tool makers early in the 19th century, was a mechanic with superior ability who had been employed at the Royal Arsenal, Woolwich. He was hired away by Joseph Bramah for the production of high security metal locks that required precision craftsmanship. Bramah patented a lathe that had similarities to the slide rest lathe. Maudslay perfected the slide rest lathe, which could cut machine screws of different thread pitches by using changeable gears between the spindle and the lead screw. Before its invention screws could not be cut to any precision using various earlier lathe designs, some of which copied from a template.[14][29]:392–95 The slide rest lathe was called one of history's most important inventions, although not entirely Maudslay's idea.[14]:31, 36
Maudslay left Bramah's employment and set up his own shop. He was engaged to build the machinery for making ships' pulley blocks for the Royal Navy in the Portsmouth Block Mills. These machines were all-metal and were the first machines for mass production and making components with a degree of interchangeability. The lessons Maudslay learned about the need for stability and precision he adapted to the development of machine tools, and in his workshops he trained a generation of men to build on his work, such as Richard Roberts, Joseph Clement and Joseph Whitworth.
James Fox of Derby had a healthy export trade in machine tools for the first third of the century, as did Matthew Murray of Leeds. Roberts was a maker of high-quality machine tools and a pioneer of the use of jigs and gauges for precision workshop measurement.
The impact of machine tools during the Industrial Revolution was not that great because other than firearms, threaded fasteners and a few other industries there were few mass-produced metal parts.[44] In the half century following the invention of the fundamental machine tools the machine industry became the largest industrial sector of the economy, by value added, in the U.S.[45]
Chemicals
The large scale production of chemicals was an important development during the Industrial Revolution. The first of these was the production of sulphuric acid by the lead chamber process invented by the Englishman John Roebuck (James Watt's first partner) in 1746. He was able to greatly increase the scale of the manufacture by replacing the relatively expensive glass vessels formerly used with larger, less expensive chambers made of riveted sheets of lead. Instead of making a small amount each time, he was able to make around 100 pounds (50 kg) in each of the chambers, at least a tenfold increase.
The production of an alkali on a large scale became an important goal as well, and Nicolas Leblanc succeeded in 1791 in introducing a method for the production of sodium carbonate. The Leblanc process was a reaction of sulphuric acid with sodium chloride to give sodium sulphate and hydrochloric acid. The sodium sulphate was heated with limestone (calcium carbonate) and coal to give a mixture of sodium carbonate and calcium sulphide. Adding water separated the soluble sodium carbonate from the calcium sulphide. The process produced a large amount of pollution (the hydrochloric acid was initially vented to the air, and calcium sulphide was a useless waste product). Nonetheless, this synthetic soda ash proved economical compared to that from burning specific plants (barilla) or from kelp, which were the previously dominant sources of soda ash,[46] and also to potash (potassium carbonate) derived from hardwood ashes.
These two chemicals were very important because they enabled the introduction of a host of other inventions, replacing many small-scale operations with more cost-effective and controllable processes. Sodium carbonate had many uses in the glass, textile, soap, and paper industries. Early uses for sulphuric acid included pickling (removing rust) iron and steel, and for bleaching cloth.
The development of bleaching powder (calcium hypochlorite) by Scottish chemist Charles Tennant in about 1800, based on the discoveries of French chemist Claude Louis Berthollet, revolutionised the bleaching processes in the textile industry by dramatically reducing the time required (from months to days) for the traditional process then in use, which required repeated exposure to the sun in bleach fields after soaking the textiles with alkali or sour milk. Tennant's factory at St Rollox, North Glasgow, became the largest chemical plant in the world.
After 1860 the focus on chemical innovation was in dyestuffs, and Germany took world leadership, building a strong chemical industry.[47] Aspiring chemists flocked to German universities in the 1860–1914 era to learn the latest techniques. British scientists by contrast, lacked research universities and did not train advanced students; instead the practice was to hire German-trained chemists.[48]
Cement
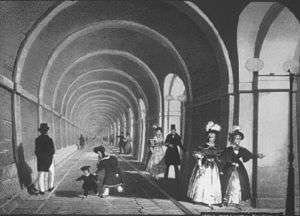
In 1824 Joseph Aspdin, a British bricklayer turned builder, patented a chemical process for making portland cement which was an important advance in the building trades. This process involves sintering a mixture of clay and limestone to about 1,400 °C (2,552 °F), then grinding it into a fine powder which is then mixed with water, sand and gravel to produce concrete. Portland cement was used by the famous English engineer Marc Isambard Brunel several years later when constructing the Thames Tunnel.[49] Cement was used on a large scale in the construction of the London sewerage system a generation later.
Gas lighting
Another major industry of the later Industrial Revolution was gas lighting. Though others made a similar innovation elsewhere, the large-scale introduction of this was the work of William Murdoch, an employee of Boulton & Watt, the Birmingham steam engine pioneers. The process consisted of the large-scale gasification of coal in furnaces, the purification of the gas (removal of sulphur, ammonia, and heavy hydrocarbons), and its storage and distribution. The first gas lighting utilities were established in London between 1812 and 1820. They soon became one of the major consumers of coal in the UK. Gas lighting affected social and industrial organisation because it allowed factories and stores to remain open longer than with tallow candles or oil. Its introduction allowed nightlife to flourish in cities and towns as interiors and streets could be lighted on a larger scale than before.
Glass making

A new method of producing glass, known as the cylinder process, was developed in Europe during the early 19th century. In 1832 this process was used by the Chance Brothers to create sheet glass. They became the leading producers of window and plate glass. This advancement allowed for larger panes of glass to be created without interruption, thus freeing up the space planning in interiors as well as the fenestration of buildings. The Crystal Palace is the supreme example of the use of sheet glass in a new and innovative structure.
Paper machine
A machine for making a continuous sheet of paper on a loop of wire fabric was patented in 1798 by Nicholas Louis Robert who worked for Saint-Léger Didot family in France. The paper machine is known as a Fourdrinier after the financiers, brothers Sealy and Henry Fourdrinier, who were stationers in London. Although greatly improved and with many variations, the Fourdriner machine is the predominant means of paper production today.
The method of continuous production demonstrated by the paper machine influenced the development of continuous rolling of iron and later steel and other continuous production processes.[50]
Agriculture
The British Agricultural Revolution is considered one of the causes of the Industrial Revolution because improved agricultural productivity freed up workers to work in other sectors of the economy.[51]
Industrial technologies that affected farming included the seed drill, the Dutch plough, which contained iron parts, and the threshing machine.
Jethro Tull invented an improved seed drill in 1701. It was a mechanical seeder which distributed seeds evenly across a plot of land and planted them at the correct depth. This was important because the yield of seeds harvested to seeds planted at that time was around four or five. Tull's seed drill was very expensive and not very reliable and therefore did not have much of an impact. Good quality seed drills were not produced until the mid 18th century.[52]
Joseph Foljambe's Rotherham plough of 1730, was the first commercially successful iron plough.[53][54][55][56] The threshing machine, invented by Andrew Meikle in 1784, displaced hand threshing with a flail, a laborious job that took about one-quarter of agricultural labour.[57]:286 It took several decades to diffuse[58] and was the final straw for many farm labourers, who faced near starvation, leading to the 1830 agricultural rebellion of the Swing Riots.
Machine tools and metalworking techniques developed during the Industrial Revolution eventually resulted in precision manufacturing techniques in the late 19th century for mass-producing agricultural equipment, such as reapers, binders and combine harvesters.[44]
Mining
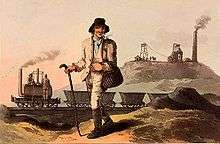
Coal mining in Britain, particularly in South Wales started early. Before the steam engine, pits were often shallow bell pits following a seam of coal along the surface, which were abandoned as the coal was extracted. In other cases, if the geology was favourable, the coal was mined by means of an adit or drift mine driven into the side of a hill. Shaft mining was done in some areas, but the limiting factor was the problem of removing water. It could be done by hauling buckets of water up the shaft or to a sough (a tunnel driven into a hill to drain a mine). In either case, the water had to be discharged into a stream or ditch at a level where it could flow away by gravity. The introduction of the steam pump by Savery in 1698 and the Newcomen steam engine in 1712 greatly facilitated the removal of water and enabled shafts to be made deeper, enabling more coal to be extracted. These were developments that had begun before the Industrial Revolution, but the adoption of John Smeaton's improvements to the Newcomen engine followed by James Watt's more efficient steam engines from the 1770s reduced the fuel costs of engines, making mines more profitable.
Coal mining was very dangerous owing to the presence of firedamp in many coal seams. Some degree of safety was provided by the safety lamp which was invented in 1816 by Sir Humphry Davy and independently by George Stephenson. However, the lamps proved a false dawn because they became unsafe very quickly and provided a weak light. Firedamp explosions continued, often setting off coal dust explosions, so casualties grew during the entire 19th century. Conditions of work were very poor, with a high casualty rate from rock falls.
Other developments
Other developments included more efficient water wheels, based on experiments conducted by the British engineer John Smeaton[59] the beginnings of a machine industry[14][60] and the rediscovery of concrete (based on hydraulic lime mortar) by John Smeaton, which had been lost for 1300 years.[61]
Transportation
At the beginning of the Industrial Revolution, inland transport was by navigable rivers and roads, with coastal vessels employed to move heavy goods by sea. Wagon ways were used for conveying coal to rivers for further shipment, but canals had not yet been widely constructed. Animals supplied all of the motive power on land, with sails providing the motive power on the sea. The first horse railways were introduced toward the end of the 18th century, with steam locomotives being introduced in the early decades of the 19th century.
The Industrial Revolution improved Britain's transport infrastructure with a turnpike road network, a canal and waterway network, and a railway network. Raw materials and finished products could be moved more quickly and cheaply than before. Improved transportation also allowed new ideas to spread quickly.
Canals
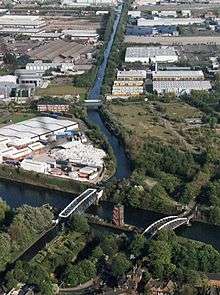
Canals were the first technology to allow bulk materials to be economically transported long distances inland. This was because a horse could pull a barge with a load dozens of times larger than the load that could be drawn in a cart.[29][62]
Building of canals dates to ancient times. The Grand Canal in China, "the world's largest artificial waterway and oldest canal still in existence," parts of which were started between the 6th and 4th centuries BC, is 1,121 miles (1,804 km) long and links Hangzhou with Beijing.[63]
In the UK, canals began to be built in the late 18th century to link the major manufacturing centres across the country. Known for its huge commercial success, the Bridgewater Canal in North West England, which opened in 1761 and was mostly funded by The 3rd Duke of Bridgewater. From Worsley to the rapidly growing town of Manchester its construction cost £168,000 (£22,589,130 as of 2013),[64][65] but its advantages over land and river transport meant that within a year of its opening in 1761, the price of coal in Manchester fell by about half.[66] This success helped inspire a period of intense canal building, known as Canal Mania.[67] New canals were hastily built in the aim of replicating the commercial success of the Bridgewater Canal, the most notable being the Leeds and Liverpool Canal and the Thames and Severn Canal which opened in 1774 and 1789 respectively.
By the 1820s a national network was in existence. Canal construction served as a model for the organisation and methods later used to construct the railways. They were eventually largely superseded as profitable commercial enterprises by the spread of the railways from the 1840s on. The last major canal to be built in the United Kingdom was the Manchester Ship Canal, which upon opening in 1894 was the largest ship canal in the world,[68] and opened Manchester as a port. However it never achieved the commercial success its sponsors had hoped for and signalled canals as a dying mode of transport in an age dominated by railways, which were quicker and often cheaper.
Britain's canal network, together with its surviving mill buildings, is one of the most enduring features of the early Industrial Revolution to be seen in Britain.
Roads

Much of the original British road system was poorly maintained by thousands of local parishes, but from the 1720s (and occasionally earlier) turnpike trusts were set up to charge tolls and maintain some roads. Increasing numbers of main roads were turnpiked from the 1750s to the extent that almost every main road in England and Wales was the responsibility of a turnpike trust. New engineered roads were built by John Metcalf, Thomas Telford and most notably John McAdam, with the first 'macadamised' stretch of road being Marsh Road at Ashton Gate, Bristol in 1816.[70] The major turnpikes radiated from London and were the means by which the Royal Mail was able to reach the rest of the country. Heavy goods transport on these roads was by means of slow, broad wheeled, carts hauled by teams of horses. Lighter goods were conveyed by smaller carts or by teams of pack horse. Stage coaches carried the rich, and the less wealthy could pay to ride on carriers carts.
Railways

Reducing friction was one of the major reasons for the success of railroads compared to wagons. This was demonstrated on an iron plate covered wooden tramway in 1805 at Croydon, England.
“ A good horse on an ordinary turnpike road can draw two thousand pounds, or one ton. A party of gentlemen were invited to witness the experiment, that the superiority of the new road might be established by ocular demonstration. Twelve wagons were loaded with stones, till each wagon weighed three tons, and the wagons were fastened together. A horse was then attached, which drew the wagons with ease, six miles in two hours, having stopped four times, in order to show he had the power of starting, as well as drawing his great load.”[71]
Railways were made practical by the widespread introduction of inexpensive puddled iron after 1800, the rolling mill for making rails, and the development of the high pressure steam engine also around 1800.
Wagonways for moving coal in the mining areas had started in the 17th century and were often associated with canal or river systems for the further movement of coal. These were all horse drawn or relied on gravity, with a stationary steam engine to haul the wagons back to the top of the incline. The first applications of the steam locomotive were on wagon or plate ways (as they were then often called from the cast-iron plates used). Horse-drawn public railways did not begin until the early years of the 19th century when improvements to pig and wrought iron production were lowering costs. See: Metallurgy
Steam locomotives began being built after the introduction of high pressure steam engines after the expiration of the Boulton and Watt patent in 1800. High pressure engines exhausted used steam to the atmosphere, doing away with the condenser and cooling water. They were also much lighter weight and smaller in size for a given horsepower than the stationary condensing engines. A few of these early locomotives were used in mines. Steam-hauled public railways began with the Stockton and Darlington Railway in 1825.
The rapid introduction of railways followed the 1829 Rainhill Trials, which demonstrated Robert Stephenson's successful locomotive design and the 1828 development of Hot blast, which dramatically reduced the fuel consumption of making iron and increased the capacity the blast furnace.
On 15 September 1830, the Liverpool and Manchester Railway was opened, the first inter-city railway in the world and was attended by Prime Minister, the Duke of Wellington.[72] The railway was engineered by Joseph Locke and George Stephenson, linked the rapidly expanding industrial town of Manchester with the port town of Liverpool. The opening was marred by problems, due to the primitive nature of the technology being employed, however problems were gradually ironed out and the railway became highly successful, transporting passengers and freight. The success of the inter-city railway, particularly in the transport of freight and commodities, led to Railway Mania.
Construction of major railways connecting the larger cities and towns began in the 1830s but only gained momentum at the very end of the first Industrial Revolution. After many of the workers had completed the railways, they did not return to their rural lifestyles but instead remained in the cities, providing additional workers for the factories.
Social effects
Factory system
Prior to the Industrial Revolution most of the workforce was employed in agriculture, either as self-employed farmers as land owners or tenants, or as landless agricultural labourers. By the time of the Industrial Revolution the putting-out system whereby farmers and townspeople produced goods in their homes, often described as cottage industry, was the standard. Typical putting out system goods included spinning and weaving. Merchant capitalist provided the raw materials, typically paid workers by the piece, and were responsible for the sale of the goods. Embezzlement of supplies by workers and poor quality were common problems. The logistical effort in procuring and distributing raw materials and picking up finished goods were also limitations of the putting out system.[73]
Some early spinning and weaving machinery, such as a 40 spindle jenny for about six pounds in 1792, was affordable for cottagers.[74] Later machinery such as spinning frames, spinning mules and power looms were expensive (especially if water powered), giving rise to capitalist ownership of factories. Many workers, who had nothing but their labour to sell, became factory workers out of necessity.
The change in the social relationship of the factory worker compared to farmers and cottagers was viewed unfavourably by Karl Marx, however, he recognized the increase in productivity made possible by technology.[75]
Impact on women and family life
Women's historians have debated the effect of the Industrial Revolution and capitalism generally on the status of women.[76][77] Taking a pessimistic side, Alice Clark argued that when capitalism arrived in 17th century England, it lowered the status of women as they lost much of their economic importance. Clark argues that in 16th century England, women were engaged in many aspects of industry and agriculture. The home was a central unit of production and women played a vital role in running farms, and in some trades and landed estates. Their useful economic roles gave them a sort of equality with their husbands. However, Clark argues, as capitalism expanded in the 17th century, there was more and more division of labour with the husband taking paid labour jobs outside the home, and the wife reduced to unpaid household work. Middle-class and women were confined to an idle domestic existence, supervising servants; lower-class women were forced to take poorly paid jobs. Capitalism, therefore, had a negative effect on powerful women.[78]
In a more positive interpretation, Ivy Pinchbeck argues that capitalism created the conditions for women's emancipation.[79] Tilly and Scott have emphasised the continuity in the status of women, finding three stages in English history. In the pre-industrial era, production was mostly for home use and women produce much of the needs of the households. The second stage was the "family wage economy" of early industrialisation; the entire family depended on the collective wages of its members, including husband, wife and older children. The third or modern stage is the "family consumer economy," in which the family is the site of consumption, and women are employed in large numbers in retail and clerical jobs to support rising standards of consumption.[80]
Standards of living
The effects on living conditions the industrial revolution have been very controversial, and were hotly debated by economic and social historians from the 1950s to the 1980s.[81] A series of 1950s essays by Henry Phelps Brown and Sheila V. Hopkins later set the academic consensus that the bulk of the population, that was at the bottom of the social ladder, suffered severe reductions in their living standards.[81] During 1813–1913, there was a significant increase in worker wages.[82][83][84]
Some economists, such as Robert E. Lucas, Jr., say that the real impact of the Industrial Revolution was that "for the first time in history, the living standards of the masses of ordinary people have begun to undergo sustained growth ... Nothing remotely like this economic behaviour is mentioned by the classical economists, even as a theoretical possibility."[3] Others, however, argue that while growth of the economy's overall productive powers was unprecedented during the Industrial Revolution, living standards for the majority of the population did not grow meaningfully until the late 19th and 20th centuries, and that in many ways workers' living standards declined under early capitalism: for instance, studies have shown that real wages in Britain only increased 15% between the 1780s and 1850s, and that life expectancy in Britain did not begin to dramatically increase until the 1870s.[4][5]
Food and nutrition
Chronic hunger and malnutrition were the norm for the majority of the population of the world including Britain and France, until the late 19th century. Until about 1750, in large part due to malnutrition, life expectancy in France was about 35 years, and only slightly higher in Britain. The United States population of the time was adequately fed, much taller on average and had life expectancy of 45–50 years.[85]
In Britain and the Netherlands, food supply had been increasing and prices falling before the Industrial Revolution due to better agricultural practices; however, population grew too, as noted by Thomas Malthus.[21]>[57][86][87] Before the Industrial Revolution, advances in agriculture or technology soon led to an increase in population, which again strained food and other resources, limiting increases in per capita income. This condition is called the Malthusian trap, and it was finally overcome by industrialisation.[57]
Transportation improvements, such as canals and improved roads, also lowered food costs. Railroads were introduced near the end of the Industrial Revolution.
Housing
Living conditions during the Industrial Revolution varied from splendour for factory owners to squalor for workers.
In The Condition of the Working Class in England in 1844 Friedrich Engels described backstreet sections of Manchester and other mill towns, where people lived in crude shanties and shacks, some not completely enclosed, some with dirt floors. These shanty towns had narrow walkways between irregularly shaped lots and dwellings. There were no sanitary facilities. Population density was extremely high. Eight to ten unrelated mill workers often shared a room, often with no furniture, and slept on a pile of straw or sawdust.[88] Toilet facilities were shared if they existed. Disease spread through a contaminated water supply. Also, people were at risk of developing pathologies due to persistent dampness.
The famines that troubled rural areas did not happen in industrial areas. But urban people—especially small children—died due to diseases spreading through the cramped living conditions. Tuberculosis (spread in congested dwellings), lung diseases from the mines, cholera from polluted water and typhoid were also common.
Not everyone lived in such poor conditions. The Industrial Revolution also created a middle class of professionals, such as lawyers and doctors, who lived in much better conditions.
Conditions improved over the course of the 19th century due to new public health acts regulating things such as sewage, hygiene and home construction. In the introduction of his 1892 edition, Engels notes that most of the conditions he wrote about in 1844 had been greatly improved.
Clothing and consumer goods
Consumers benefited from falling prices for clothing and household articles such as cast iron cooking utensils, and in the following decades, stoves for cooking and space heating.
Population increase
According to Robert Hughes in The Fatal Shore, the population of England and Wales, which had remained steady at six million from 1700 to 1740, rose dramatically after 1740. The population of England had more than doubled from 8.3 million in 1801 to 16.8 million in 1850 and, by 1901, had nearly doubled again to 30.5 million.[89] Improved conditions led to the population of Britain increasing from 10 million to 40 million in the 1800s.[90][91] Europe's population increased from about 100 million in 1700 to 400 million by 1900.[92]
The Industrial Revolution was the first period in history during which there was a simultaneous increase in both population and per capita income.[93]
Labour conditions
Social structure and working conditions
In terms of social structure, the Industrial Revolution witnessed the triumph of a middle class of industrialists and businessmen over a landed class of nobility and gentry. Ordinary working people found increased opportunities for employment in the new mills and factories, but these were often under strict working conditions with long hours of labour dominated by a pace set by machines. As late as the year 1900, most industrial workers in the United States still worked a 10-hour day (12 hours in the steel industry), yet earned from 20% to 40% less than the minimum deemed necessary for a decent life.[94] However, harsh working conditions were prevalent long before the Industrial Revolution took place. Pre-industrial society was very static and often cruel—child labour, dirty living conditions, and long working hours were just as prevalent before the Industrial Revolution.[95]
Factories and urbanisation

Industrialisation led to the creation of the factory. Arguably the first highly mechanised was John Lombe's water-powered silk mill at Derby, operational by 1721. Lombe learned silk thread manufacturing by taking a job in Italy and acting as an industrial spy; however, since the silk industry there was a closely guarded secret, the state of the industry there is unknown. Because Lombe's factory was not successful and there was no follow through, the rise of the modern factory dates to somewhat later when cotton spinning was mechanised.
The factory system contributed to the growth of urban areas, as large numbers of workers migrated into the cities in search of work in the factories. Nowhere was this better illustrated than the mills and associated industries of Manchester, nicknamed "Cottonopolis", and the world's first industrial city.[96] Manchester experienced a six-times increase in its population between 1771 and 1831. Bradford grew by 50% every ten years between 1811 and 1851 and by 1851 only 50% of the population of Bradford was actually born there.[97]
For much of the 19th century, production was done in small mills, which were typically water-powered and built to serve local needs. Later, each factory would have its own steam engine and a chimney to give an efficient draft through its boiler.
The transition to industrialisation was not without difficulty. For example, a group of English workers known as Luddites formed to protest against industrialisation and sometimes sabotaged factories.
In other industries the transition to factory production was not so divisive. Some industrialists themselves tried to improve factory and living conditions for their workers. One of the earliest such reformers was Robert Owen, known for his pioneering efforts in improving conditions for workers at the New Lanark mills, and often regarded as one of the key thinkers of the early socialist movement.
By 1746 an integrated brass mill was working at Warmley near Bristol. Raw material went in at one end, was smelted into brass and was turned into pans, pins, wire, and other goods. Housing was provided for workers on site. Josiah Wedgwood and Matthew Boulton (whose Soho Manufactory was completed in 1766) were other prominent early industrialists, who employed the factory system.
Child labour

The Industrial Revolution led to a population increase but the chances of surviving childhood did not improve throughout the Industrial Revolution, although infant mortality rates were reduced markedly.[99][100] There was still limited opportunity for education and children were expected to work. Employers could pay a child less than an adult even though their productivity was comparable; there was no need for strength to operate an industrial machine, and since the industrial system was completely new, there were no experienced adult labourers. This made child labour the labour of choice for manufacturing in the early phases of the Industrial Revolution between the 18th and 19th centuries. In England and Scotland in 1788, two-thirds of the workers in 143 water-powered cotton mills were described as children.[101]
Child labour existed before the Industrial Revolution but with the increase in population and education it became more visible. Many children were forced to work in relatively bad conditions for much lower pay than their elders,[102] 10–20% of an adult male's wage.[103] Children as young as four were employed.[103] Beatings and long hours were common, with some child coal miners and hurriers working from 4 am until 5 pm.[103] Conditions were dangerous, with some children killed when they dozed off and fell into the path of the carts, while others died from gas explosions.[103] Many children developed lung cancer and other diseases and died before the age of 25.[103] Workhouses would sell orphans and abandoned children as "pauper apprentices", working without wages for board and lodging.[103] Those who ran away would be whipped and returned to their masters, with some masters shackling them to prevent escape.[103] Children employed as mule scavengers by cotton mills would crawl under machinery to pick up cotton, working 14 hours a day, six days a week. Some lost hands or limbs, others were crushed under the machines, and some were decapitated.[103] Young girls worked at match factories, where phosphorus fumes would cause many to develop phossy jaw.[103] Children employed at glassworks were regularly burned and blinded, and those working at potteries were vulnerable to poisonous clay dust.[103]
Reports were written detailing some of the abuses, particularly in the coal mines[104] and textile factories,[105] and these helped to popularise the children's plight. The public outcry, especially among the upper and middle classes, helped stir change in the young workers' welfare.
Politicians and the government tried to limit child labour by law but factory owners resisted; some felt that they were aiding the poor by giving their children money to buy food to avoid starvation, and others simply welcomed the cheap labour. In 1833 and 1844, the first general laws against child labour, the Factory Acts, were passed in Britain: Children younger than nine were not allowed to work, children were not permitted to work at night, and the work day of youth under the age of 18 was limited to twelve hours. Factory inspectors supervised the execution of the law, however, their scarcity made enforcement difficult.[103] About ten years later, the employment of children and women in mining was forbidden. These laws decreased the number of child labourers, however child labour remained in Europe and the United States up to the 20th century.[106]
Luddites
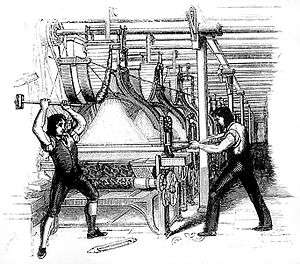
The rapid industrialisation of the English economy cost many craft workers their jobs. The movement started first with lace and hosiery workers near Nottingham and spread to other areas of the textile industry owing to early industrialisation. Many weavers also found themselves suddenly unemployed since they could no longer compete with machines which only required relatively limited (and unskilled) labour to produce more cloth than a single weaver. Many such unemployed workers, weavers and others, turned their animosity towards the machines that had taken their jobs and began destroying factories and machinery. These attackers became known as Luddites, supposedly followers of Ned Ludd, a folklore figure. The first attacks of the Luddite movement began in 1811. The Luddites rapidly gained popularity, and the British government took drastic measures, using the militia or army to protect industry. Those rioters who were caught were tried and hanged, or transported for life.
Unrest continued in other sectors as they industrialised, such as with agricultural labourers in the 1830s when large parts of southern Britain were affected by the Captain Swing disturbances. Threshing machines were a particular target, and hayrick burning was a popular activity. However, the riots led to the first formation of trade unions, and further pressure for reform.
Organisation of labour
The Industrial Revolution concentrated labour into mills, factories and mines, thus facilitating the organisation of combinations or trade unions to help advance the interests of working people. The power of a union could demand better terms by withdrawing all labour and causing a consequent cessation of production. Employers had to decide between giving in to the union demands at a cost to themselves or suffering the cost of the lost production. Skilled workers were hard to replace, and these were the first groups to successfully advance their conditions through this kind of bargaining.
The main method the unions used to effect change was strike action. Many strikes were painful events for both sides, the unions and the management. In Britain, the Combination Act 1799 forbade workers to form any kind of trade union until its repeal in 1824. Even after this, unions were still severely restricted.
In 1832, the Reform Act extended the vote in Britain but did not grant universal suffrage. That year six men from Tolpuddle in Dorset founded the Friendly Society of Agricultural Labourers to protest against the gradual lowering of wages in the 1830s. They refused to work for less than ten shillings a week, although by this time wages had been reduced to seven shillings a week and were due to be further reduced to six. In 1834 James Frampton, a local landowner, wrote to the Prime Minister, Lord Melbourne, to complain about the union, invoking an obscure law from 1797 prohibiting people from swearing oaths to each other, which the members of the Friendly Society had done. James Brine, James Hammett, George Loveless, George's brother James Loveless, George's brother in-law Thomas Standfield, and Thomas's son John Standfield were arrested, found guilty, and transported to Australia. They became known as the Tolpuddle Martyrs. In the 1830s and 1840s, the Chartist movement was the first large-scale organised working class political movement which campaigned for political equality and social justice. Its Charter of reforms received over three million signatures but was rejected by Parliament without consideration.
Working people also formed friendly societies and co-operative societies as mutual support groups against times of economic hardship. Enlightened industrialists, such as Robert Owen also supported these organisations to improve the conditions of the working class.
Unions slowly overcame the legal restrictions on the right to strike. In 1842, a general strike involving cotton workers and colliers was organised through the Chartist movement which stopped production across Great Britain.[107]
Eventually, effective political organisation for working people was achieved through the trades unions who, after the extensions of the franchise in 1867 and 1885, began to support socialist political parties that later merged to become the British Labour Party.
Impact on environment
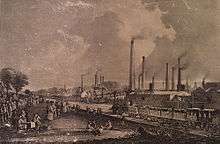
The origins of the environmental movement lay in the response to increasing levels of smoke pollution in the atmosphere during the Industrial Revolution. The emergence of great factories and the concomitant immense growth in coal consumption gave rise to an unprecedented level of air pollution in industrial centers; after 1900 the large volume of industrial chemical discharges added to the growing load of untreated human waste.[108] The first large-scale, modern environmental laws came in the form of Britain's Alkali Acts, passed in 1863, to regulate the deleterious air pollution (gaseous hydrochloric acid) given off by the Leblanc process, used to produce soda ash. An Alkali inspector and four sub-inspectors were appointed to curb this pollution. The responsibilities of the inspectorate were gradually expanded, culminating in the Alkali Order 1958 which placed all major heavy industries that emitted smoke, grit, dust and fumes under supervision.
The manufactured gas industry began in British cities in 1812–1820. The technique used produced highly toxic effluent that was dumped into sewers and rivers. The gas companies were repeatedly sued in nuisance lawsuits. They usually lost and modified the worst practices. The City of London repeatedly indicted gas companies in the 1820s for polluting the Thames and poisoning its fish. Finally, Parliament wrote company charters to regulate toxicity.[109] The industry reached the US around 1850 causing pollution and lawsuits.[110]
In industrial cities local experts and reformers, especially after 1890, took the lead in identifying environmental degradation and pollution, and initiating grass-roots movements to demand and achieve reforms.[111] Typically the highest priority went to water and air pollution. The Coal Smoke Abatement Society was formed in Britain in 1898 making it one of the oldest environmental NGOs. It was founded by artist Sir William Blake Richmond, frustrated with the pall cast by coal smoke. Although there were earlier pieces of legislation, the Public Health Act 1875 required all furnaces and fireplaces to consume their own smoke. It also provided for sanctions against factories that emitted large amounts of black smoke. The provisions of this law were extended in 1926 with the Smoke Abatement Act to include other emissions, such as soot, ash and gritty particles and to empower local authorities to impose their own regulations.[112]
Other effects
The application of steam power to the industrial processes of printing supported a massive expansion of newspaper and popular book publishing, which reinforced rising literacy and demands for mass political participation.
During the Industrial Revolution, the life expectancy of children increased dramatically. The percentage of the children born in London who died before the age of five decreased from 74.5% in 1730–1749 to 31.8% in 1810–1829.[99]
The growth of modern industry since the late 18th century led to massive urbanisation and the rise of new great cities, first in Europe and then in other regions, as new opportunities brought huge numbers of migrants from rural communities into urban areas. In 1800, only 3% of the world's population lived in cities,[113] compared to nearly 50% today (the beginning of the 21st century).[114] Manchester had a population of 10,000 in 1717, but by 1911 it had burgeoned to 2.3 million.[115]
Industrialisation beyond the United Kingdom
Continental Europe
Eric Hobsbawm held that the Industrial Revolution began in Britain in the 1780s and was not fully felt until the 1830s or 1840s,[6] while T. S. Ashton held that it occurred roughly between 1760 and 1830.[7] The Industrial Revolution on Continental Europe came a little later than in Great Britain. In many industries, this involved the application of technology developed in Britain in new places. Often the technology was purchased from Britain or British engineers and entrepreneurs moved abroad in search of new opportunities. By 1809, part of the Ruhr Valley in Westphalia was called 'Miniature England' because of its similarities to the industrial areas of England. The German, Russian and Belgian governments all provided state funding to the new industries. In some cases (such as iron), the different availability of resources locally meant that only some aspects of the British technology were adopted.
Belgium
Belgium was the second country, after Britain, in which the Industrial Revolution took place and the first in continental Europe: Wallonia (French speaking southern Belgium) was the first region to follow the British model successfully. Starting in the middle of the 1820s, and especially after Belgium became an independent nation in 1830, numerous works comprising coke blast furnaces as well as puddling and rolling mills were built in the coal mining areas around Liège and Charleroi. The leader was a transplanted Englishman John Cockerill. His factories at Seraing integrated all stages of production, from engineering to the supply of raw materials, as early as 1825.[116]
Wallonia exemplified the radical evolution of industrial expansion. Thanks to coal (the French word "houille" was coined in Wallonia),[117] the region geared up to become the 2nd industrial power in the world after Britain. But it is also pointed out by many researchers, with its Sillon industriel, 'Especially in the Haine, Sambre and Meuse valleys, between the Borinage and Liège, (...) there was a huge industrial development based on coal-mining and iron-making...'.[118] Philippe Raxhon wrote about the period after 1830: "It was not propaganda but a reality the Walloon regions were becoming the second industrial power all over the world after Britain."[119] "The sole industrial centre outside the collieries and blast furnaces of Walloon was the old cloth making town of Ghent."[120] Michel De Coster, Professor at the Université de Liège wrote also: "The historians and the economists say that Belgium was the second industrial power of the world, in proportion to its population and its territory (...) But this rank is the one of Wallonia where the coal-mines, the blast furnaces, the iron and zinc factories, the wool industry, the glass industry, the weapons industry... were concentrated." [121]
Demographic effects
Wallonia was also the birthplace of a strong Socialist party and strong trade-unions in a particular sociological landscape. At the left, the Sillon industriel, which runs from Mons in the west, to Verviers in the east (except part of North Flanders, in another period of the industrial revolution, after 1920). Even if Belgium is the second industrial country after Britain, the effect of the industrial revolution there was very different. In 'Breaking stereotypes', Muriel Neven and Isabelle Devious say:
The industrial revolution changed a mainly rural society into an urban one, but with a strong contrast between northern and southern Belgium. During the Middle Ages and the Early Modern Period, Flanders was characterised by the presence of large urban centres (...) at the beginning of the nineteenth century this region (Flanders), with an urbanisation degree of more than 30 per cent, remained one of the most urbanised in the world. By comparison, this proportion reached only 17 per cent in Wallonia, barely 10 per cent in most West European countries, 16 per cent in France and 25 per cent in Britain. Nineteenth century industrialisation did not affect the traditional urban infrastructure, except in Ghent (...) Also, in Wallonia the traditional urban network was largely unaffected by the industrialisation process, even though the proportion of city-dwellers rose from 17 to 45 per cent between 1831 and 1910. Especially in the Haine, Sambre and Meuse valleys, between the Borinage and Liège, where there was a huge industrial development based on coal-mining and iron-making, urbanisation was fast. During these eighty years the number of municipalities with more than 5,000 inhabitants increased from only 21 to more than one hundred, concentrating nearly half of the Walloon population in this region. Nevertheless, industrialisation remained quite traditional in the sense that it did not lead to the growth of modern and large urban centres, but to a conurbation of industrial villages and towns developed around a coal-mine or a factory. Communication routes between these small centres only became populated later and created a much less dense urban morphology than, for instance, the area around Liège where the old town was there to direct migratory flows.[122]
France
The industrial revolution in France followed a particular course as it did not correspond to the main model followed by other countries. Notably, most French historians argue France did not go through a clear take-off.[123] Instead, France's economic growth and industrialisation process was slow and steady through the 18th and 19th centuries. However, some stages were identified by Maurice Lévy-Leboyer:
- French Revolution and Napoleonic wars (1789–1815),
- industrialisation, along with Britain (1815–1860),
- economic slowdown (1860–1905),
- renewal of the growth after 1905.
Germany
Based on its leadership in chemical research in the universities and industrial laboratories, Germany, which was unified in 1871, became dominant in the world's chemical industry in the late 19th century. At first the production of dyes based on aniline was critical.[124]
Germany's political disunity—with three dozen states—and a pervasive conservatism made it difficult to build railways in the 1830s. However, by the 1840s, trunk lines linked the major cities; each German state was responsible for the lines within its own borders. Lacking a technological base at first, the Germans imported their engineering and hardware from Britain, but quickly learned the skills needed to operate and expand the railways. In many cities, the new railway shops were the centres of technological awareness and training, so that by 1850, Germany was self-sufficient in meeting the demands of railroad construction, and the railways were a major impetus for the growth of the new steel industry. Observers found that even as late as 1890, their engineering was inferior to Britain's. However, German unification in 1870 stimulated consolidation, nationalisation into state-owned companies, and further rapid growth. Unlike the situation in France, the goal was support of industrialisation, and so heavy lines crisscrossed the Ruhr and other industrial districts, and provided good connections to the major ports of Hamburg and Bremen. By 1880, Germany had 9,400 locomotives pulling 43,000 passengers and 30,000 tons of freight, and pulled ahead of France[125]
Sweden
During the period 1790–1815 Sweden experienced two parallel economic movements: an agricultural revolution with larger agricultural estates, new crops and farming tools and a commercialisation of farming, and a protoindustrialisation, with small industries being established in the countryside and with workers switching between agricultural work in summer and industrial production in winter. This led to economic growth benefiting large sections of the population and leading up to a consumption revolution starting in the 1820s.
During 1815–1850 the protoindustries developed into more specialised and larger industries. This period witnessed increasing regional specialisation with mining in Bergslagen, textile mills in Sjuhäradsbygden and forestry in Norrland. Several important institutional changes took place in this period, such as free and mandatory schooling introduced 1842 (as first country in the world), the abolition of the national monopoly on trade in handicrafts in 1846, and a stock company law in 1848.
During 1850–1890, Sweden experienced a veritable explosion in export, dominated by crops, wood and steel. Sweden abolished most tariffs and other barriers to free trade in the 1850s and joined the gold standard in 1873.
During 1890–1930, Sweden experienced the second industrial revolution. New industries developed with their focus on the domestic market: mechanical engineering, power utilities, papermaking and textile.
United States
During the late 18th an early 19th centuries when the UK and parts of Western Europe began to industrialise, the US was primarily an agricultural and natural resource producing and processing economy.[126] The building of roads and canals, the introduction of steamboats and the building of railroads were important for handling agricultural and natural resource products in the large and sparsely populated country of the period.[127][128]
Important American technological contributions during the period of the Industrial Revolution were the cotton gin and the development of a system for making interchangeable parts, the latter aided by the development of the milling machine in the US. The development of machine tools and the system of interchangeable parts were the basis for the rise of the US as the world's leading industrial nation in the late 19th century.
Oliver Evans invented an automated flour mill in the mid 1780s that used control mechanisms and conveyors so that no labour was needed from the time grain was loaded into the elevator buckets until flour was discharged into a wagon. This is considered to be the first modern materials handling system an important advance in the progress toward mass production.[44]
The United States originally used horse-powered machinery for small scale applications such as grain milling, but eventually switched to water power after textile factories began being built in the 1790s. As a result, industrialisation was concentrated in New England and the Northeastern United States, which has fast-moving rivers. The newer water-powered production lines proved more economical than horse-drawn production. In the late 19th century steam-powered manufacturing overtook water-powered manufacturing, allowing the industry to spread to the Midwest.
Thomas Somers and the Cabot Brothers founded the Beverly Cotton Manufactory in 1787, the first cotton mill in America, the largest cotton mill of its era,[129] and a significant milestone in the research and development of cotton mills in the future. This mill was designed to use horse power, but the operators quickly learned that the horse-drawn platform was economically unstable, and had economic losses for years. Despite the losses, the Manufactory served as a playground of innovation, both in turning a large amount of cotton, but also developing the water-powered milling structure used in Slater's Mill.[130]
In 1793, Samuel Slater (1768–1835) founded the Slater Mill at Pawtucket, Rhode Island. He had learned of the new textile technologies as a boy apprentice in Derbyshire, England, and defied laws against the emigration of skilled workers by leaving for New York in 1789, hoping to make money with his knowledge. After founding Slater's Mill, he went on to own 13 textile mills.[131] Daniel Day established a wool carding mill in the Blackstone Valley at Uxbridge, Massachusetts in 1809, the third woollen mill established in the US (The first was in Hartford, Connecticut, and the second at Watertown, Massachusetts.) The John H. Chafee Blackstone River Valley National Heritage Corridor retraces the history of "America's Hardest-Working River', the Blackstone. The Blackstone River and its tributaries, which cover more than 45 miles (72 km) from Worcester, Massachusetts to Providence, Rhode Island, was the birthplace of America's Industrial Revolution. At its peak over 1100 mills operated in this valley, including Slater's mill, and with it the earliest beginnings of America's Industrial and Technological Development.
Merchant Francis Cabot Lowell from Newburyport, Massachusetts memorised the design of textile machines on his tour of British factories in 1810. Realising that the War of 1812 had ruined his import business but that a demand for domestic finished cloth was emerging in America, on his return to the United States, he set up the Boston Manufacturing Company. Lowell and his partners built America's second cotton-to-cloth textile mill at Waltham, Massachusetts, second to the Beverly Cotton Manufactory. After his death in 1817, his associates built America's first planned factory town, which they named after him. This enterprise was capitalised in a public stock offering, one of the first uses of it in the United States. Lowell, Massachusetts, using 5.6 miles (9.0 km) of canals and 10,000 horsepower delivered by the Merrimack River, is considered by some as a major contributor to the success of the American Industrial Revolution. The short-lived utopia-like Waltham-Lowell system was formed, as a direct response to the poor working conditions in Britain. However, by 1850, especially following the Irish Potato Famine, the system had been replaced by poor immigrant labour.
The industrialisation of the watch industry started 1854 also in Waltham, Massachusetts, at the Waltham Watch Company, with the development of machine tools, gauges and assembling methods adapted to the micro precision required for watches.
Japan
The industrial revolution began about 1870 as Meiji period leaders decided to catch up with the West. The government built railroads, improved roads, and inaugurated a land reform programme to prepare the country for further development. It inaugurated a new Western-based education system for all young people, sent thousands of students to the United States and Europe, and hired more than 3,000 Westerners to teach modern science, mathematics, technology, and foreign languages in Japan (O-yatoi gaikokujin).
In 1871, a group of Japanese politicians known as the Iwakura Mission toured Europe and the United States to learn western ways. The result was a deliberate state-led industrialisation policy to enable Japan to quickly catch up. The Bank of Japan, founded in 1882,[132] used taxes to fund model steel and textile factories. Education was expanded and Japanese students were sent to study in the west.
Modern industry first appeared in textiles, including cotton and especially silk, which was based in home workshops in rural areas.[133]
Second Industrial Revolution
.jpg)
Steel is often cited as the first of several new areas for industrial mass-production, which are said to characterise a "Second Industrial Revolution", beginning around 1850, although a method for mass manufacture of steel was not invented until the 1860s, when Sir Henry Bessemer invented a new furnace which could convert molten pig iron into steel in large quantities. However, it only became widely available in the 1870s after the process was modified to produce more uniform quality.[29][134] Bessemer steel was being displaced by the open hearth furnace near the end of the 19th century.
This Second Industrial Revolution gradually grew to include chemicals, mainly the chemical industries, petroleum (refining and distribution), and, in the 20th century, the automotive industry, and was marked by a transition of technological leadership from Britain to the United States and Germany.
The increasing availability of economical petroleum products also reduced the importance of coal and further widened the potential for industrialisation.
A new revolution began with electricity and electrification in the electrical industries. The introduction of hydroelectric power generation in the Alps enabled the rapid industrialisation of coal-deprived northern Italy, beginning in the 1890s.
By the 1890s, industrialisation in these areas had created the first giant industrial corporations with burgeoning global interests, as companies like U.S. Steel, General Electric, Standard Oil and Bayer AG joined the railroad and ship companies on the world's stock markets.
Opposition from Romanticism
During the Industrial Revolution an intellectual and artistic hostility towards the new industrialisation developed, associated with the Romantic movement. Romanticism revered the traditionalism of rural life and recoiled against the upheavals caused by industrialization, urbanization and the wretchedness of the working classes.[135] Its major exponents in English included the artist and poet William Blake and poets William Wordsworth, Samuel Taylor Coleridge, John Keats, Lord Byron and Percy Bysshe Shelley. The movement stressed the importance of "nature" in art and language, in contrast to "monstrous" machines and factories; the "Dark satanic mills" of Blake's poem "And did those feet in ancient time". Mary Shelley's novel Frankenstein reflected concerns that scientific progress might be two-edged. French Romanticisim likewise was highly critical of industry.[136]
Causes
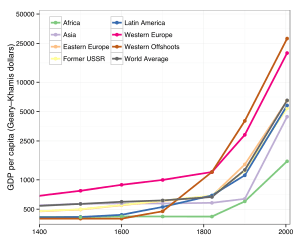
The causes of the Industrial Revolution were complicated and remain a topic for debate, with some historians believing the Revolution was an outgrowth of social and institutional changes brought by the end of feudalism in Britain after the English Civil War in the 17th century. The Enclosure movement and the British Agricultural Revolution made food production more efficient and less labour-intensive, forcing the surplus population who could no longer find employment in agriculture into cottage industry, for example weaving, and in the longer term into the cities and the newly developed factories.[137] The colonial expansion of the 17th century with the accompanying development of international trade, creation of financial markets and accumulation of capital are also cited as factors, as is the scientific revolution of the 17th century.[138]
Until the 1980s, it was universally believed by academic historians that technological innovation was the heart of the Industrial Revolution and the key enabling technology was the invention and improvement of the steam engine.[139] However, recent research into the Marketing Era has challenged the traditional, supply-oriented interpretation of the Industrial Revolution.[140]
Lewis Mumford has proposed that the Industrial Revolution had its origins in the Early Middle Ages, much earlier than most estimates.[141] He explains that the model for standardised mass production was the printing press and that "the archetypal model for the industrial era was the clock". He also cites the monastic emphasis on order and time-keeping, as well as the fact that medieval cities had at their centre a church with bell ringing at regular intervals as being necessary precursors to a greater synchronisation necessary for later, more physical, manifestations such as the steam engine.
The presence of a large domestic market should also be considered an important driver of the Industrial Revolution, particularly explaining why it occurred in Britain. In other nations, such as France, markets were split up by local regions, which often imposed tolls and tariffs on goods traded among them.[142] Internal tariffs were abolished by Henry VIII of England, they survived in Russia till 1753, 1789 in France and 1839 in Spain.
Governments' grant of limited monopolies to inventors under a developing patent system (the Statute of Monopolies in 1623) is considered an influential factor. The effects of patents, both good and ill, on the development of industrialisation are clearly illustrated in the history of the steam engine, the key enabling technology. In return for publicly revealing the workings of an invention the patent system rewarded inventors such as James Watt by allowing them to monopolise the production of the first steam engines, thereby rewarding inventors and increasing the pace of technological development. However, monopolies bring with them their own inefficiencies which may counterbalance, or even overbalance, the beneficial effects of publicising ingenuity and rewarding inventors.[143] Watt's monopoly may have prevented other inventors, such as Richard Trevithick, William Murdoch or Jonathan Hornblower, from introducing improved steam engines, thereby retarding the industrial revolution by about 16 years.[144][145]
Causes in Europe
.jpg)
European 17th century colonial expansion, international trade, and creation of financial markets produced a new legal and financial environment, one which supported and enabled 18th century industrial growth.
One question of active interest to historians is why the Industrial Revolution occurred in Europe and not in other parts of the world in the 18th century, particularly China, India, and the Middle East, or at other times like in Classical Antiquity[146] or the Middle Ages.[147] Numerous factors have been suggested, including education, technological changes[148] (see Scientific Revolution in Europe), "modern" government, "modern" work attitudes, ecology, and culture.[149] However, most historians contest the assertion that Europe and China were roughly equal because modern estimates of per capita income on Western Europe in the late 18th century are of roughly 1,500 dollars in purchasing power parity (and Britain had a per capita income of nearly 2,000 dollars[150]) whereas China, by comparison, had only 450 dollars.
Some historians such as David Landes and Max Weber credit the different belief systems in Asia and Europe with dictating where the revolution occurred.[151] The religion and beliefs of Europe were largely products of Judaeo-Christianity and Greek thought. Conversely, Chinese society was founded on men like Confucius, Mencius, Han Feizi (Legalism), Lao Tzu (Taoism), and Buddha (Buddhism), resulting in very different worldviews.[152] Other factors include the considerable distance of China's coal deposits, though large, from its cities as well as the then unnavigable Yellow River that connects these deposits to the sea.[153]
Regarding India, the Marxist historian Rajani Palme Dutt said: "The capital to finance the Industrial Revolution in India instead went into financing the Industrial Revolution in Britain."[154] In contrast to China, India was split up into many competing kingdoms, with the three major ones being the Marathas, Sikhs and the Mughals. In addition, the economy was highly dependent on two sectors—agriculture of subsistence and cotton, and there appears to have been little technical innovation. It is believed that the vast amounts of wealth were largely stored away in palace treasuries by totalitarian monarchs prior to the British take over.
Causes in Britain

Great Britain provided the legal and cultural foundations that enabled entrepreneurs to pioneer the industrial revolution.[155] Key factors fostering this environment were: (1) The period of peace and stability which followed the unification of England and Scotland; (2) no trade barriers between England and Scotland; (3) the rule of law (respecting the sanctity of contracts); (4) a straightforward legal system which allowed the formation of joint-stock companies (corporations); and (5) a free market (capitalism).[21]
Geographical and natural resource advantages of Great Britain were the fact that it had extensive coast lines and many navigable rivers in an age where water was the easiest means of transportation and having the highest quality coal in Europe.[21]
There were two main values that really drove the Industrial Revolution in Britain. These values were self-interest and an entrepreneurial spirit. Because of these interests, many industrial advances were made that resulted in a huge increase in personal wealth. These advancements also greatly benefitted the British society as a whole. Countries around the world started to recognise the changes and advancements in Britain and use them as an example to begin their own Industrial Revolutions.[156]
The debate about the start of the Industrial Revolution also concerns the massive lead that Great Britain had over other countries. Some have stressed the importance of natural or financial resources that Britain received from its many overseas colonies or that profits from the British slave trade between Africa and the Caribbean helped fuel industrial investment. However, it has been pointed out that slave trade and West Indian plantations provided only 5% of the British national income during the years of the Industrial Revolution.[157] Even though slavery accounted for so little, Caribbean-based demand accounted for 12% of Britain's industrial output.[158]

Instead, the greater liberalisation of trade from a large merchant base may have allowed Britain to produce and use emerging scientific and technological developments more effectively than countries with stronger monarchies, particularly China and Russia. Britain emerged from the Napoleonic Wars as the only European nation not ravaged by financial plunder and economic collapse, and having the only merchant fleet of any useful size (European merchant fleets were destroyed during the war by the Royal Navy[159]). Britain's extensive exporting cottage industries also ensured markets were already available for many early forms of manufactured goods. The conflict resulted in most British warfare being conducted overseas, reducing the devastating effects of territorial conquest that affected much of Europe. This was further aided by Britain's geographical position—an island separated from the rest of mainland Europe.
Another theory is that Britain was able to succeed in the Industrial Revolution due to the availability of key resources it possessed. It had a dense population for its small geographical size. Enclosure of common land and the related agricultural revolution made a supply of this labour readily available. There was also a local coincidence of natural resources in the North of England, the English Midlands, South Wales and the Scottish Lowlands. Local supplies of coal, iron, lead, copper, tin, limestone and water power, resulted in excellent conditions for the development and expansion of industry. Also, the damp, mild weather conditions of the North West of England provided ideal conditions for the spinning of cotton, providing a natural starting point for the birth of the textiles industry.
The stable political situation in Britain from around 1688, and British society's greater receptiveness to change (compared with other European countries) can also be said to be factors favouring the Industrial Revolution. Peasant resistance to industrialisation was largely eliminated by the Enclosure movement, and the landed upper classes developed commercial interests that made them pioneers in removing obstacles to the growth of capitalism.[160] (This point is also made in Hilaire Belloc's The Servile State.)
Britain's population grew 280% 1550–1820, while the rest of Western Europe grew 50–80%. Seventy percent of European urbanisation happened in Britain 1750–1800. By 1800, only the Netherlands was more urbanised than Britain. This was only possible because coal, coke, imported cotton, brick and slate had replaced wood, charcoal, flax, peat and thatch. The latter compete with land grown to feed people while mined materials do not. Yet more land would be freed when chemical fertilisers replaced manure and horse's work was mechanised. A workhorse needs 3 to 5 acres (1.21 to 2.02 ha) for fodder while even early steam engines produced four times more mechanical energy.
In 1700, 5/6 of coal mined worldwide was in Britain, while the Netherlands had none; so despite having Europe's best transport, most urbanised, well paid, literate people and lowest taxes, it failed to industrialise. In the 18th century, it was the only European country whose cities and population shrank. Without coal, Britain would have run out of suitable river sites for mills by the 1830s.[161]
Transfer of knowledge

Knowledge of innovation was spread by several means. Workers who were trained in the technique might move to another employer or might be poached. A common method was for someone to make a study tour, gathering information where he could. During the whole of the Industrial Revolution and for the century before, all European countries and America engaged in study-touring; some nations, like Sweden and France, even trained civil servants or technicians to undertake it as a matter of state policy. In other countries, notably Britain and America, this practice was carried out by individual manufacturers eager to improve their own methods. Study tours were common then, as now, as was the keeping of travel diaries. Records made by industrialists and technicians of the period are an incomparable source of information about their methods.
Another means for the spread of innovation was by the network of informal philosophical societies, like the Lunar Society of Birmingham, in which members met to discuss 'natural philosophy' (i.e. science) and often its application to manufacturing. The Lunar Society flourished from 1765 to 1809, and it has been said of them, "They were, if you like, the revolutionary committee of that most far reaching of all the eighteenth century revolutions, the Industrial Revolution".[162] Other such societies published volumes of proceedings and transactions. For example, the London-based Royal Society of Arts published an illustrated volume of new inventions, as well as papers about them in its annual Transactions.
There were publications describing technology. Encyclopaedias such as Harris's Lexicon Technicum (1704) and Abraham Rees's Cyclopaedia (1802–1819) contain much of value. Cyclopaedia contains an enormous amount of information about the science and technology of the first half of the Industrial Revolution, very well illustrated by fine engravings. Foreign printed sources such as the Descriptions des Arts et Métiers and Diderot's Encyclopédie explained foreign methods with fine engraved plates.
Periodical publications about manufacturing and technology began to appear in the last decade of the 18th century, and many regularly included notice of the latest patents. Foreign periodicals, such as the Annales des Mines, published accounts of travels made by French engineers who observed British methods on study tours.
Protestant work ethic
Another theory is that the British advance was due to the presence of an entrepreneurial class which believed in progress, technology and hard work.[163] The existence of this class is often linked to the Protestant work ethic (see Max Weber) and the particular status of the Baptists and the dissenting Protestant sects, such as the Quakers and Presbyterians that had flourished with the English Civil War. Reinforcement of confidence in the rule of law, which followed establishment of the prototype of constitutional monarchy in Britain in the Glorious Revolution of 1688, and the emergence of a stable financial market there based on the management of the national debt by the Bank of England, contributed to the capacity for, and interest in, private financial investment in industrial ventures.
Dissenters found themselves barred or discouraged from almost all public offices, as well as education at England's only two universities at the time (although dissenters were still free to study at Scotland's four universities). When the restoration of the monarchy took place and membership in the official Anglican Church became mandatory due to the Test Act, they thereupon became active in banking, manufacturing and education. The Unitarians, in particular, were very involved in education, by running Dissenting Academies, where, in contrast to the universities of Oxford and Cambridge and schools such as Eton and Harrow, much attention was given to mathematics and the sciences—areas of scholarship vital to the development of manufacturing technologies.
Historians sometimes consider this social factor to be extremely important, along with the nature of the national economies involved. While members of these sects were excluded from certain circles of the government, they were considered fellow Protestants, to a limited extent, by many in the middle class, such as traditional financiers or other businessmen. Given this relative tolerance and the supply of capital, the natural outlet for the more enterprising members of these sects would be to seek new opportunities in the technologies created in the wake of the scientific revolution of the 17th century.
See also
- General
- Capitalist mode of production
- Deindustrialization
- Division of labour
- Dual revolution
- Economic history of the United Kingdom
- Capitalism in the nineteenth century
- Human timeline
- Industrial Age
- Information revolution
- Law of the handicap of a head start – Dialectics of progress
- Machine Age
- The Protestant Ethic and the Spirit of Capitalism
- Other
References
- 1 2 David S. Landes (1969). The Unbound Prometheus. Press Syndicate of the University of Cambridge. p. 40. ISBN 0-521-09418-6.
- ↑ Baten, Jörg (2016). A History of the Global Economy. From 1500 to the Present. Cambridge University Press. p. 13-16. ISBN 9781107507180.
- 1 2 Lucas, Robert E., Jr. (2002). Lectures on Economic Growth. Cambridge: Harvard University Press. pp. 109–10. ISBN 978-0-674-01601-9.
- 1 2 Feinstein, Charles (September 1998). "Pessimism Perpetuated: Real Wages and the Standard of Living in Britain during and after the Industrial Revolution". Journal of Economic History. 58 (3): 625–58. doi:10.1017/s0022050700021100. Retrieved 6 May 2014.
- 1 2 Szreter & Mooney; Mooney (February 1998). "Urbanization, Mortality, and the Standard of Living Debate: New Estimates of the Expectation of Life at Birth in Nineteenth-Century British Cities". The Economic History Review. 51 (1): 104. doi:10.1111/1468-0289.00084. Retrieved 6 May 2014.
- 1 2 Eric Hobsbawm, The Age of Revolution: Europe 1789–1848, Weidenfeld & Nicolson Ltd., p. 27 ISBN 0-349-10484-0
- 1 2 Joseph E Inikori. Africans and the Industrial Revolution in England, Cambridge University Press. ISBN 0-521-01079-9 Read it
- ↑ Berg, Maxine; Hudson, Pat (1992). "Rehabilitating the Industrial Revolution". The Economic History Review. The Economic History Review, Vol. 45, No. 1. 45 (1): 24–50. doi:10.2307/2598327. JSTOR 2598327.
- ↑ Rehabilitating the Industrial Revolution by Julie Lorenzen, Central Michigan University. Retrieved November 2006.
- ↑ Robert Lucas, Jr. (2003). "The Industrial Revolution". Federal Reserve Bank of Minneapolis. Archived from the original on 27 November 2007. Retrieved 14 November 2007.
it is fairly clear that up to 1800 or maybe 1750, no society had experienced sustained growth in per capita income. (Eighteenth century population growth also averaged one-third of 1 percent, the same as production growth.) That is, up to about two centuries ago, per capita incomes in all societies were stagnated at around $400 to $800 per year.
- ↑ Lucas, Robert (2003). "The Industrial Revolution Past and Future". Archived from the original on 27 November 2007.
[consider] annual growth rates of 2.4 percent for the first 60 years of the 20th century, of 1 percent for the entire 19th century, of one-third of 1 percent for the 18th century
- ↑ McCloskey, Deidre (2004). "Review of The Cambridge Economic History of Modern Britain (edited by Roderick Floud and Paul Johnson), Times Higher Education Supplement, 15 January 2004".
- ↑ Taylor, George Rogers. The Transportation Revolution, 1815–1860. ISBN 978-0-87332-101-3. No name is given to the transition years. The Transportation Revolution began with improved roads in the late 18th century.
- 1 2 3 4 5 6 Roe, Joseph Wickham (1916), English and American Tool Builders, New Haven, Connecticut: Yale University Press, LCCN 16011753. Reprinted by McGraw-Hill, New York and London, 1926 (LCCN 27-24075); and by Lindsay Publications, Inc., Bradley, Illinois, (ISBN 978-0-917914-73-7).
- ↑ Hunter 1985
- ↑ Crouzet, François (1996). "France". In Teich, Mikuláš; Porter, Roy. The industrial revolution in national context: Europe and the USA. Cambridge University Press. p. 45. ISBN 978-0-521-40940-7. LCCN 95025377.
- ↑ BLANQUI Jérôme-Adolphe, Histoire de l'économie politique en Europe depuis les anciens jusqu'à nos jours, 1837, ISBN 978-0-543-94762-8
- ↑ Hudson, Pat (1992). The Industrial Revolution. London: Edward Arnold. p. 11. ISBN 978-0-7131-6531-9.
- ↑ Eric Bond; Sheena Gingerich; Oliver Archer-Antonsen; Liam Purcell; Elizabeth Macklem (17 February 2003). "The Industrial Revolution – Innovations". Industrialrevolution.sea.ca. Retrieved 30 January 2011.
- ↑ Ayres 1989, pp. 17
- 1 2 3 4 5 6 David S. Landes (1969). The Unbound Prometheus. Press Syndicate of the University of Cambridge. p. 00. ISBN 0-521-09418-6.
- 1 2 David S. Landes (1969). The Unbound Prometheus. Press Syndicate of the University of Cambridge. p. 82. ISBN 0-521-09418-6.
- ↑ Hunter year-1985
- ↑ David S. Landes (1969). The Unbound Prometheus. Press Syndicate of the University of Cambridge. pp. 89–93. ISBN 0-521-09418-6.
- ↑ David S. Landes (1969). The Unbound Prometheus. Press Syndicate of the University of Cambridge. p. 218. ISBN 0-521-09418-6.
- ↑ Rosen, William (2012). The Most Powerful Idea in the World: A Story of Steam, Industry and Invention. University Of Chicago Press. p. 149. ISBN 978-0-226-72634-2.
- 1 2 David S. Landes (1969). The Unbound Prometheus. Press Syndicate of the University of Cambridge. p. 91. ISBN 0-521-09418-6.
- 1 2 3 Ayres, Robert (1989). "Technological Transformations and Long Waves" (PDF): 16–17.
- 1 2 3 4 5 6 7 8 9 10 McNeil 1990
- ↑ R. Ray Gehani (1998). "Management of Technology and Operations". P. 63. John Wiley and Sons, 1998
- ↑ Ayres 1989, pp. 1
- ↑ David S. Landes (1969). The Unbound Prometheus. Press Syndicate of the University of Cambridge. p. 63. ISBN 0-521-09418-6.
- ↑ Ayres 1989, pp. 18
- ↑ "You've Got Luddites All Wrong". vice.com.
- ↑ G. E. Mingay (1986). "The Transformation of Britain, 1830–1939". p. 25. Routledge, 1986
- ↑ Gordon, Robert B (1996). American Iron 1607–1900. Baltimore and London: Johns Hopkins University Press. p. 156. ISBN 0-8018-6816-5.
- ↑ Landes year-1969, pp. 218
- ↑ David S. Landes (1969). The Unbound Prometheus. Press Syndicate of the University of Cambridge. p. 92. ISBN 0-521-09418-6.
- ↑ Ayres 1989, pp. 21
- ↑ Rosenberg, Nathan (1982). Inside the Black Box: Technology and Economics. Cambridge, New York: Cambridge University Press. p. 90. ISBN 0-521-27367-6.
- ↑ David S. Landes (1969). The Unbound Prometheus. Press Syndicate of the University of Cambridge. p. 104. ISBN 0-521-09418-6.
- ↑ Hunter&Bryant 1991
- ↑ Rolt and Allen, 145
- 1 2 3 Hounshell, David A. (1984), From the American System to Mass Production, 1800-1932: The Development of Manufacturing Technology in the United States, Baltimore, Maryland: Johns Hopkins University Press, ISBN 978-0-8018-2975-8, LCCN 83016269
- ↑ Economics 323-2: Economic History of the United States Since 1865 http://faculty.wcas.northwestern.edu/~jmokyr/Graphs-and-Tables.PDF
- ↑ Clow, Archibald; Clow, Nan L. (June 1952). "Chemical Revolution". Ayer Co: 65–90. ISBN 0-8369-1909-2.
- ↑ Lion Hirth, State, Cartels and Growth: The German Chemical Industry (2007) p 20
- ↑ Johann P. Murmann, Knowledge and competitive advantage: the co-evolution of firms, technology, and national institutions (2003) pp 53–54
- ↑ Properties of Concrete Published lecture notes from University of Memphis Department of Civil Engineering. Retrieved 17 October 2007.
- ↑ Misa, Thomas J. (1995). A Nation of Steel: The Making of Modern America 1965–1925. Baltimore and London: Johns Hopkins University Press. p. 243. ISBN 978-0-8018-6502-2.
- ↑ Overton, Mark (1996). Agricultural Revolution in England: The transformation if the agrarian economy 1500–1850. Cambridge University Press. ISBN 978-0-521-56859-3.
- ↑ Temple 1986, pp. 26
- ↑ Overton 1996, pp. 122
- ↑ "The Rotherham Plow". Rotherham: The Unofficial Website.
- ↑ Temple 1986, pp. 18, 20
- ↑ "The Rotherham Plow". Rotherham.co.uk.
- 1 2 3 Clark 2007
- ↑ Atack, Jeremy; Passell, Peter (1994). A New Economic View of American History. New York: W.W. Norton and Co. p. 282. ISBN 0-393-96315-2.
- ↑ Rosen, William (2012). The Most Powerful Idea in the World: A Story of Steam, Industry and Invention. University Of Chicago Press. p. 127. ISBN 978-0-226-72634-2.
- ↑ Musson; Robinson (1969). Science and Technology in the Industrial Revolution. University of Toronto Press. p. 477.
- ↑ Encyclopædia Britannica (2008) "Building construction: the reintroduction of modern concrete"
- ↑ Grübler, Arnulf (1990). The Rise and Fall of Infrastructures: Dynamics of Evolution and Technological Change in Transport (PDF). Heidelberg and New York: Physica-Verlag.
- ↑ Donald Langmead. Encyclopedia of Architectural and Engineering Feats. ABC-CLIO. p. 37. ISBN 978-1-57607-112-0. Retrieved 15 February 2013.
- ↑ UK CPI inflation numbers based on data available from Gregory Clark (2016), "The Annual RPI and Average Earnings for Britain, 1209 to Present (New Series)" MeasuringWorth.
- ↑ Timbs 1860, p. 363
- ↑ The Times newspaper: Bridgewater Collieries, London, 1 December 1913, retrieved 19 July 2008
- ↑ Kindleberger 1993, pp. 192–193
- ↑ "1 January 1894: Opening of the Manchester ship canal". The Guardian. 1 January 1894. Retrieved 28 July 2012.
Six years in the making, the world's largest navigation canal gives the city direct access to the sea
- ↑ "1823 – First American Macadam Road" (Painting – Carl Rakeman) US Department of Transportation – Federal Highway Administration (Accessed 10 October 2008)
- ↑ Richard Brown (1991). "Society and Economy in Modern Britain 1700–1850" p. 136. Routledge, 1991
- ↑ Fling, Harry M. (1868). Railroads of the United States, Their History and Statistics. Philadelphia: John. E. Potter and Co. pp. 12, 13.
- ↑ Herbert L. Sussman (2009). "Victorian Technology: Invention, Innovation, and the Rise of the Machine". p. 2. ABC-CLIO, 2009
- ↑ Landes year-1969, pp. 57–9
- ↑ Landes year-1969, pp. 59
- ↑ Hunt, E. K.; Lautzenheiser, Mark (2014). History of Economic Thought: A Critical Perspective. PHI Learning. ISBN 978-0765625991.
- ↑ Eleanor Amico, ed. Reader's guide to women's studies (1998) pp 102–4, 306–8.
- ↑ Janet Thomas, "Women and capitalism: oppression or emancipation? A review article." Comparative studies in society and history 30#3 (1988): 534–549. in JSTOR
- ↑ Alice Clark, Working life of women in the seventeenth century (1919).
- ↑ Ivy Pinchbeck, Women Workers in the Industrial Revolution (1930).
- ↑ Louise Tilly and Joan Wallach Scott, Women, work, and family (1987).
- 1 2 Woodward, D. (1981) Wage rates and living standards in pre-industrial England Past & Present 1981 91(1):28–46
- ↑ Crafts, N; Mills, Terence C. (1994). "Trends in Real Wages in Britain, 1750–1913". Explorations in Economic History. 31 (2): 176. doi:10.1006/exeh.1994.1007.
- ↑ Industrial Revolution and the Standard of Living From www.econlib.org, downloaded 17 July 2006.
- ↑ R.M. Hartwell, The Rising Standard of Living in England, 1800–1850, Economic History Review, 1963, page 398 ISBN 0-631-18071-0
- ↑ Fogel, Robert W. (2004). The Escape from Hunger and Premature Death, 1700–2100. London: Cambridge University Press. ISBN 0-521-80878-2.
- ↑ Malthus, Thomas (1798). An Essay on the Principle of Population (PDF). London. Retrieved 2016-02-12.
- ↑ Temple, Robert; Needham, Joseph (1986). The Genius of China: 3000 years of science, discovery and invention. New York: Simon and Schuster<Based on the works of Joseph Needham>
- ↑ Engels, Friedrich (1892). The Condition of the Working-Class in England in 1844. London: Swan Sonnenschein & Co. pp. 45, 48–53.
- ↑ "The UK population: past, present and future – Chapter 1" (PDF). Statistics.gov.uk
- ↑ "A portrait of Britain in 2031". The Independent. 24 October 2007.
- ↑ BBC – History – Victorian Medicine – From Fluke to Theory. Published: 1 February 2002.
- ↑ "Modernization – Population Change". Encyclopædia Britannica.
- ↑ Hudson, Pat (1992). The Industrial Revolution. New York: Routledge, Chapman and Hall, Inc. p. 3. ISBN 0-7131-6531-6.
- ↑ "United States History – The Struggles of Labor". Library of Congress Country Studies.
- ↑ R.M. Hartwell, The Industrial Revolution and Economic Growth, Methuen and Co., 1971, page 339–341 ISBN 0-416-19500-8
- ↑ "Manchester – the first industrial city". Entry on Sciencemuseum website. Archived from the original on 9 March 2012. Retrieved 17 March 2012.
- ↑ "Life in Industrial Towns".
- ↑ Dunn, James (1905). From Coal Mine Upwards: or Seventy Years of an Eventful Life. ISBN 1-4344-6870-4.
- 1 2 Mabel C. Buer, Health, Wealth and Population in the Early Days of the Industrial Revolution, London: George Routledge & Sons, 1926, page 30 ISBN 0-415-38218-1
- ↑ Bar, Michael; Leukhina, Oksana (2007). "Demographic Transition and Industrial Revolution: A Macroeconomic Investigation" (PDF). Archived from the original (PDF) on 27 November 2007. Retrieved 5 November 2007.
The decrease [in mortality] beginning in the second half of the 18th century was due mainly to declining adult mortality. Sustained decline of the mortality rates for the age groups 5–10, 10–15, and 15–25 began in the mid-19th century, while that for the age group 0–5 began three decades later
. Although the survival rates for infants and children were static over this period, the birth rate & overall life expectancy increased. Thus the population grew, but the average Briton was about as old in 1850 as in 1750 (see figures 5 & 6, page 28). Population size statistics from mortality.org put the mean age at about 26. - ↑ "Child Labour and the Division of Labour in the Early English Cotton Mills". Douglas A. Galbi. Centre for History and Economics, King's College, Cambridge CB2 1ST.
- ↑ The Life of the Industrial Worker in Nineteenth-Century England, Laura Del Col, West Virginia University.
- 1 2 3 4 5 6 7 8 9 10 11 Venning, Annabel (17 September 2010). "Britain's child slaves: They started at 4am, lived off acorns and had nails put through their ears for shoddy work. Yet, says a new book, their misery helped forge Britain". dailymail.co.uk. London. Retrieved 19 September 2010.
- ↑ "Testimony Gathered by Ashley's Mines Commission". 2008. Retrieved 22 March 2008.
- ↑ "The Life of the Industrial Worker in Nineteenth-Century England". 2008. Retrieved 22 March 2008.
- ↑ "Photographs of Lewis Hine: Documentation of Child Labor". The U.S. National Archives and Records Administration.
- ↑ "General Strike 1842". Archived from the original on 9 June 2007. Retrieved 2007-06-09. From chartists.net. Retrieved 13 November 2006.
- ↑ Fleming, James R.; Bethany R. Knorr. "History of the Clean Air Act". American Meteorological Society. Retrieved 2006-02-14.
- ↑ Leslie Tomory, "The Environmental History of the Early British Gas Industry, 1812–1830." Environmental history 17#1 (2012): 29–54.
- ↑ Joel A. Tarr, "Toxic Legacy: The Environmental Impact of the Manufactured Gas Industry in the United States." Technology and culture 55#1 (2014): 107–147. online
- ↑ Harold L. Platt, Shock cities: the environmental transformation and reform of Manchester and Chicago (2005) excerpt.
- ↑ Brian William Clapp, An environmental history of Britain since the industrial revolution (Routledge, 2014).
- ↑ "Human Population: Urbanization". Population Reference Bureau. Archived 26 October 2009 at the Wayback Machine.
- ↑ "Human Population: Population Growth: Question and Answer". Population Reference Bureau. Archived 8 October 2009 at the Wayback Machine.
- ↑ Manchester (England, United Kingdom). Encyclopædia Britannica.
- ↑ Chris Evans, Göran Rydén, The Industrial Revolution in Iron; The impact of British Coal Technology in Ninenteenth-Century Europe Published by Ashgate Publishing, Ltd., Farnham2005, pp. 37–38 ISBN 0-7546-3390-X.
- ↑ a word from Walloon origin
- ↑ Muriel Neven and Isabelle Devos, 'Breaking stereotypes', in M. Neven and I. Devos (editors), 'Recent work in Belgian Historical Demography', in Revue belge d'histoire contemporaine, XXXI, 2001, 3–4, pages 347–359 FLWI.ugent.be Archived 29 October 2008 at the Wayback Machine.
- ↑ Philippe Raxhon, Le siècle des forges ou la Wallonie dans le creuset belge (1794–1914), in B. Demoulin and JL Kupper (editors), Histoire de la Wallonie, Privat, Toulouse, 2004, pages 233–276, p. 246 ISBN 2-7089-4779-6
- ↑ "European Route of Industrial Heritage". En.erih.net. Retrieved 19 August 2013.
- ↑ Michel De Coster, Les enjeux des conflits linguistiques, L'Harmattan, Paris, 2007, ISBN 978-2-296-03394-8, pages 122–123
- ↑ Muriel Neven and Isabelle Devos, Breaking stereotypes, art. cit., pages 315–316
- ↑ Jean Marczewski, « Y a-t-il eu un "take-off" en France ? », 1961, dans les Cahiers de l'ISEA
- ↑ Haber 1958
- ↑ Allan Mitchell, Great Train Race: Railways and the Franco-German Rivalry, 1815–1914 (2000)
- ↑ Atack, Jeremy; Passell, Peter (1994). A New Economic View of American History. New York: W.W. Norton and Co. p. 469. ISBN 0-393-96315-2.
- ↑ Chandler Jr., Alfred D. (1993). The Visible Hand: The Management Revolution in American Business. Belknap Press of Harvard University Press. ISBN 978-0674940529.
- ↑ Taylor, George Rogers (1969). The Transportation Revolution, 1815–1860. ISBN 978-0873321013.
- ↑ Bagnall, William R. The Textile Industries of the United States: Including Sketches and Notices of Cotton, Woolen, Silk, and Linen Manufacturers in the Colonial Period. Vol. I. The Riverside Press, 1893.
- ↑ "Made In Beverly-A History of Beverly Industry", by Daniel J. Hoisington. A publication of the Beverly Historic District Commission. 1989.
- ↑ Encyclopædia Britannica (1998): Samuel Slater
- ↑ "History". Bank of Japan. Retrieved 5 May 2015.
- ↑ G.C. Allen, Short Economic History of Modern Japan (1972)
- ↑ Morison, Elting E. (1966). Men, Machines and Modern Times. Cambridga, Ma and London, UK: The M.I.T Press.
- ↑ Michael Löwy and Robert Sayre, eds., Romanticism against the Tide of Modernity (Duke University Press, 2001).
- ↑ AJ George, The development of French romanticism: the impact of the industrial revolution on literature (1955)
- ↑ Steven Kreis (11 October 2006). "The Origins of the Industrial Revolution in England". Historyguide.org. Retrieved 30 January 2011.
- ↑ "Scientific Revolution". Microsoft Encarta Online Encyclopedia 2009. Archived 28 October 2009 at the Wayback Machine. 31 October 2009. Archived 28 October 2009 at the Wayback Machine.
- ↑ Hudson, Pat. The Industrial Revolution, Oxford University Press US. ISBN 0-7131-6531-6
- ↑ Fullerton, Ronald A. (January 1988). "How Modern Is Modern Marketing? Marketing's Evolution and the Myth of the "Production Era"". The Journal of Marketing. New York City, NY: American Marketing Association. 52 (1): 108–125. doi:10.2307/1251689. JSTOR 1251689.
- ↑ "Technics & Civilization". Lewis Mumford. Retrieved 8 January 2009.
- ↑ Deane, Phyllis. The First Industrial Revolution, Cambridge University Press. ISBN 0-521-29609-9 Read it
- ↑ Eric Schiff, Industrialisation without national patents: the Netherlands, 1869–1912; Switzerland, 1850–1907, Princeton University Press, 1971.
- ↑ Michele Boldrin and David K. Levine, Against Intellectual Monopoly, "Chapter 1, final online version January 2, 2008" (PDF). (55 KB), page 15. Cambridge University Press, 2008. ISBN 978-0-521-87928-6
- ↑ Mott-Smith, Morton (1964) [Unabridged and revised version of the book first published by D. Appleton-Century Company in 1934 under the former title: The Story of Energy]. The Concept of Energy Simply Explained. New York: Dover Publications, Inc. pp. 13–14. ISBN 0-486-21071-5.
- ↑ Why No Industrial Revolution in Ancient Greece? J. Bradford DeLong, Professor of Economics, University of California at Berkeley, 20 September 2002. Retrieved January 2007.
- ↑ The Origins of the Industrial Revolution in England |The History Guide, Steven Kreis, 11 October 2006 – Accessed January 2007
- ↑ Jackson J. Spielvogel (2009). "Western Civilization: Since 1500". p.607.
- ↑ Eric Bond; Sheena Gingerich; Oliver Archer-Antonsen; Liam Purcell; Elizabeth Macklem (17 February 2003). "The Industrial Revolution – Causes". Industrialrevolution.sea.ca. Retrieved 30 January 2011.
- ↑ "Cobb-Douglas in pre-modern Europe1 – Simulating early modern growth" (PDF). (254 KB) Jan Luiten van Zanden, International Institute of Social History/University of Utrecht. May 2005. Retrieved January 2007.
- ↑ David S. Landes (1969). The Unbound Prometheus. Press Syndicate of the University of Cambridge. pp. 20–32. ISBN 0-521-09418-6.
- ↑ Merson 1990, pp. 34–5
- ↑ How Earth Made Us: Fire by Professor Iain Stewart
- ↑ South Asian History -Pages from the history of the Indian subcontinent: British rule and the legacy of colonisation. Rajni-Palme Dutt India Today (Indian Edition published 1947). Retrieved January 2007. Archived 27 January 2007 at the Wayback Machine.
- ↑ Julian Hoppit, "The Nation, the State, and the First Industrial Revolution," Journal of British Studies (April 2011) 50#2 pp p 307–331
- ↑ Kiely, Ray (November 2011). "Industrialization and Development: A Comparative Analysis". UGL Press Limited: 25–26.
- ↑ Digital History; Steven Mintz. "Was slavery the engine of economic growth? Digital History". Digitalhistory.uh.edu. Archived from the original on 19 February 2014. Retrieved 30 January 2011.
- ↑ The Industrial Revolution by Pat Hudson, pg. 198. Books.google.com. 1992. ISBN 978-0-7131-6531-9. Retrieved 30 January 2011.
- ↑ The Royal Navy itself may have contributed to Britain's industrial growth. Among the first complex industrial manufacturing processes to arise in Britain were those that produced material for British warships. For instance, the average warship of the period used roughly 1000 pulley fittings. With a fleet as large as the Royal Navy, and with these fittings needing to be replaced ever 4 to 5 years, this created a great demand which encouraged industrial expansion. The industrial manufacture of rope can also be see as a similar factor.
- ↑ Barrington Moore, Jr., Social Origins of Dictatorship and Democracy: Lord and Peasant in the Making of the Modern World, pp. 29–30, Boston, Beacon Press, 1966.
- ↑ E A Wrigley, Continuity chance and change.
- ↑ "The Lunar Society". Archived from the original on 7 February 2008. Retrieved 2008-02-07. at Moreabout, the website of the Birmingham Jewellery Quarter guide, Bob Miles.
- ↑ Foster, Charles (2004). Capital and Innovation: How Britain Became the First Industrial Nation. Northwich: Arley Hall Press. ISBN 0-9518382-4-5. Argues that capital accumulation and wealth concentration in an entrepreneurial culture following the commercial revolution made the industrial revolution possible, for example.
- Sources
- Ashton, Thomas S. (1948). "The Industrial Revolution (1760–1830)". Oxford University Press.
- Berlanstein, Lenard R., ed. (1992). The Industrial Revolution and work in nineteenth-century Europe. London and New York: Routledge.
- Clapham, J. H. (1926). "An Economic History of Modern Britain: The Early Railway Age, 1820–1850". Cambridge University Press.
- Clapham, J. H. The Economic Development of France and Germany 1815–1914 (1936)
- Clark, Gregory (2007). A Farewell to Alms: A Brief Economic History of the World. Princeton University Press. ISBN 0-691-12135-4.
- Daunton, M. J. (1995). "Progress and Poverty: An Economic and Social History of Britain, 1700–1850". Oxford University Press.
- Dodd, William (1847). The Laboring Classes of England : especially those engaged in agriculture and manufactures; in a series of letters. Boston: John Putnam.
- Dunham, Arthur Louis (1955). "The Industrial Revolution in France, 1815–1848". New York: Exposition Press.
- Gatrell, Peter (2004). "Farm to factory: a reinterpretation of the Soviet industrial revolution". The Economic History Review. 57 (4): 794. doi:10.1111/j.1468-0289.2004.00295_21.x.
- Griffin, Emma (2010). Short History of the British Industrial Revolution. Palgrave.
- Haber, Ludwig Fritz (1958). The Chemical Industry During the Nineteenth Century: A Study of the Economic Aspect of Applied Chemistry in Europe and North America.
- Haber, Ludwig Fritz (1971). The Chemical Industry: 1900–1930: International Growth and Technological Change.
- Jacob, Margaret C. (1997). "Scientific Culture and the Making of the Industrial West". Oxford, UK: Oxford University Press.
- Kindleberger, Charles Poor (1993). A Financial History of Western Europe. Oxford University Press US. ISBN 0-19-507738-5.
- Kisch, Herbert (1989). "From Domestic Manufacture to Industrial Revolution The Case of the Rhineland Textile Districts". Oxford University Press.
- Kornblith, Gary. The Industrial Revolution in America (1997)
- Landes, David S. (1969). The Unbound Prometheus: Technological Change and Industrial Development in Western Europe from 1750 to the Present. Cambridge, New York: Press Syndicate of the University of Cambridge. ISBN 0-521-09418-6.
- McNeil, Ian, ed. (1990). An Encyclopedia of the History of Technology. London: Routledge. ISBN 0-415-14792-1.
- Maddison, Angus (2003). "The World Economy: Historical Statistics". Paris: Organisation for Economic Co-operation and Development (OECD).
- Mantoux, Paul (1961) [1928]. "The Industrial Revolution in the Eighteenth Century" (First English translation 1928 ed.).
- McLaughlin Green, Constance (1939). "Holyoke, Massachusetts: A Case History of the Industrial Revolution in America". New Haven, CT: Yale University Press.
- Milward, Alan S. and S. B. Saul. The Development of the Economies of Continental Europe: 1850–1914 (1977)
- Milward, Alan S. and S. B. Saul. The Economic Development of Continental Europe 1780–1870 (1973)
- Mokyr, Joel (1999). "The British Industrial Revolution: An Economic Perspective".
- More, Charles (2000). "Understanding the Industrial Revolution". London: Routledge.
- Olson, James S. Encyclopedia of the Industrial Revolution in America (2001)
- Pollard, Sidney (1981). "Peaceful Conquest: The Industrialization of Europe, 1760–1970". Oxford University Press.
- Rider, Christine, ed. Encyclopedia of the Age of the Industrial Revolution, 1700–1920 (2 vol. 2007)
- Roe, Joseph Wickham (1916), English and American Tool Builders, New Haven, Connecticut: Yale University Press, LCCN 16011753. Reprinted by McGraw-Hill, New York and London, 1926 (LCCN 27-24075); and by Lindsay Publications, Inc., Bradley, Illinois, (ISBN 978-0-917914-73-7).
- Smelser, Neil J. (1959). "Social Change in the Industrial Revolution: An Application of Theory to the British Cotton Industry". University of Chicago Press.
- Staley, David J. ed. Encyclopedia of the History of Invention and Technology (3 vol 2011), 2000pp
- Stearns, Peter N. (1998). "The Industrial Revolution in World History". Westview Press.
- Smil, Vaclav (1994). "Energy in World History". Westview Press. Archived from the original on 18 July 2007.
- Snooks, G.D. (2000). "Was the Industrial Revolution Necessary?". London: Routledge.
- Szostak, Rick (1991). "The Role of Transportation in the Industrial Revolution: A Comparison of England and France". Montreal: McGill-Queen's University Press.
- Timbs, John (1860). Stories of Inventors and Discoverers in Science and the Useful Arts: A Book for Old and Young. Harper & Brothers.
- Toynbee, Arnold (1884). Lectures on the Industrial Revolution of the Eighteenth Century in England. ISBN 1-4191-2952-X. Retrieved 2016-02-12.
- Uglow, Jenny (2002). "The Lunar Men: The Friends who made the Future 1730–1810". London: Faber and Faber.
- Usher, Abbott Payson (1920). "An Introduction to the Industrial History of England". University of Michigan Press.
- Chambliss, William J. (editor), Problems of Industrial Society, Reading, Massachusetts: Addison-Wesley Publishing Co, December 1973. ISBN 978-0-201-00958-3
- Hawke, Gary. "Reinterpretations of the Industrial Revolution" in Patrick O'Brien and Roland Quinault, eds. The Industrial Revolution and British Society (1993) pp 54–78
- McCloskey, Deirdre (2004). "Review of The Cambridge Economic History of Britain (edited by Roderick Floud and Paul Johnson)". Times Higher Education Supplement. 15 (January). Retrieved 2016-02-12.
External links
![]() |
Wikimedia Commons has media related to Industrial revolution. |
![]() |
Wikiquote has quotations related to: Industrial Revolution |
![]() |
Wikiversity quiz on this Industrial Revolution article |
- Industrial Revolution at DMOZ
- Internet Modern History Sourcebook: Industrial Revolution
- BBC History Home Page: Industrial Revolution
- National Museum of Science and Industry website: machines and personalities
- Factory Workers in the Industrial Revolution
- The Industrial Revolution—Articles, Video, Pictures, and Facts
- Industrial Revolution and the Standard of Living by Clark Nardinelli – the debate over whether standards of living rose or fell.
- "The Day the World Took Off" Six-part video series from the University of Cambridge tracing the question "Why did the Industrial Revolution begin when and where it did."