Ducted fan
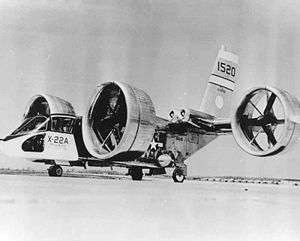
A ducted fan is a propulsion arrangement whereby a mechanical fan, which is a type of propeller, is mounted within a cylindrical shroud or duct. The duct reduces losses in thrust from the tips of the props, and varying the cross-section of the duct allows the designer to advantageously affect the velocity and pressure of the airflow according to Bernoulli's Principle. Ducted fan propulsion is used in aircraft, airships, airboats, hovercraft and fan packs.[1]
Ducted fans normally have more and shorter blades than propellers and thus can operate at higher rotational speeds.
Applications
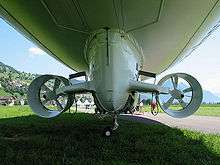
In aircraft applications, the operating speed of an unshrouded propeller is limited since tip speeds approach the sound barrier at lower speeds than an equivalent ducted fan. The most common ducted fan arrangement used in full-sized aircraft is a turbofan engine, where the power to turn the fan is provided by a gas turbine. Turbofan engines are used on nearly all airliners, fighters, and bombers. However, a ducted fan may be powered by any source of shaft power such as a reciprocating engine, Wankel engine, or electric motor. A kind of ducted fan, known as a fantail or by the trademark name Fenestron, is also used to replace tail rotors on helicopters. Ducted fans usually have an odd number of blades to prevent resonance in the duct.
_stationed_at_Little_Creek_Amphibious_Base%2C_Va.%2C_checks_the_propeller_of_a_Landing_Craft_Air_Cushion_(LCAC).jpg)
Ducted fans are favored in VTOL aircraft such as the Lockheed Martin F-35 Lightning II, and other low-speed designs such as hovercraft for their higher thrust-to-weight ratio.
In some cases, a shrouded rotor can be 94% more efficient than an open rotor. The improved performance is mainly because the outward flow is less contracted and thus carries more kinetic energy.[2]
Among model aircraft hobbyists, the ducted fan is popular with builders of high-performance radio controlled model aircraft. Internal-combustion glow engines combined with ducted-fan units were the first achievable means of modeling a scaled-size jet aircraft. Despite the introduction of model-scale turbojet engines, electric-powered ducted fans remain popular on smaller, lower-cost model aircraft. Some electric-powered ducted fan airplanes can reach speeds of more than 320km/h (200mph).
Advantages
.jpg)
- By reducing propeller blade tip losses, the ducted fan is more efficient in producing thrust than a conventional propeller of similar diameter, especially at low speed and high static thrust level (airships, hovercraft).
- By sizing the ductwork appropriately, the designer can adjust the fan to allow it to operate more efficiently at higher air speeds than a propeller would.
- For the same static thrust, a ducted fan has a smaller diameter than a free propeller, allowing smaller gear.
- Ducted fans are quieter than propellers: they shield the blade noise, and reduce the tip speed and intensity of the tip vortices both of which contribute to noise production.
- Ducted fans can allow for a limited amount of thrust vectoring, something normal propellers are not well suited for. This allows them to be used instead of tiltrotors in some applications.
- Ducted fans offer enhanced safety on the ground.
Disadvantages
- Less efficient than a propeller at cruise (at lower thrust level).
- Good efficiency requires very small clearances between the blade tips and the duct.
- Requires high RPM and minimal vibration.
- Complex duct design, and weight increase even if constructed from advanced composites.
- At high angle of attack, parts of the duct will stall and produce aerodynamic drag.[3]
See also
- Centrifugal fan
- Fan (mechanical)
- Geared turbofan
- Ducted propeller
- Pusher configuration
- Unducted fan
- Flying Car
References
- ↑ Technology Review: Fan pack
- ↑ Pereira, Jason L. Hover and wind-tunnel testing of shrouded rotors for improved micro air vehicle design p147+p11. University of Maryland, 2008. Accessed: 28 August 2015.
- ↑ Jon Longbottom - Mechanical aeronautics, thesis in PDF format