Strake

A strake or stringer is part of the shell of the hull of a boat or ship which, in conjunction with the other strakes, keeps the vessel watertight and afloat. It is a strip of planking in a wooden vessel or of plating in a metal one, running longitudinally along the vessel's side, bottom or the turn of the bilge, usually from one end of the vessel to the other. Stringers run horizontally along the ship's frame providing structural strength.[1] On a longboat, one strake will typically be made up of numerous planks running end to end.
Special strakes
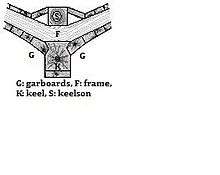
The strake immediately adjacent to the keel is known as the garboard strake. There are two, one on each side of the keel.
The uppermost continuous strake along the topsides is called the sheer strake. In old vessels, a rubbing strake was built in just below a carvel sheer strake. It was much less broad but thicker than other strakes so that it projected and took any rubbing against piers or other boats when the boat was in use. In clinker boats, the rubbing strake was applied to the outside of the sheer strake. The strakes adjacent to the garboard are referred to accordingly as the first broad and second broad. Each strake thereafter has its own special name such as bottom strakes, lowers, bilge strakes, topside strakes, and uppers. Many current pleasure craft reflect this history by providing the boat with a mechanically attached (and therefore replaceable) rub rail at the location formerly occupied by a rubbing strake, often doubling to cover the joint between a GRP hull and its innerliner.
A stealer is a short strake employed to reduce the width of plank required where the girth of the hull increases or is necessary due to a tuck in the shape. It is commonly employed in carvel and iron/steel shipbuilding, but there are very few, possibly only one type of, clinker craft that use them.
Construction
Where the transverse sections of the vessel's shape are fuller, the strakes are wider. They taper toward the ends. In many larger vessels, to avoid ending with very narrow strakes, two are normally converted to one toward their ends. This one is known as a stealer or stealer strake. It was one of these which was also shaped to fit the concave line of the hull, under the counter at the sternpost. Historically, these had to be shaped by carving from an especially thick plank of wood (known as a short strake or plank). When someone was describing the epitome of thickness, he thought of the metaphor, thick as two short planks.
In very small boats, strakes can be made of one continuous piece of wood. Usually, they are made of more than one piece of wood or metal scarfed or butted together similar to brick wall construction. In metal vessels, the modern practice is to butt-weld them with full penetration welds.
In a riveted steel ship, the strakes were usually lapped and joggled, but where a smoother finish was sought, they too might be riveted on a butt strap, though this was weaker. In modern welded construction, the plates are normally butt-welded all round to adjoining plates within the strake and to adjoining strakes.
Wooden vessels
Wooden planks can be scarfed into a strake by suitably tapering the thickness of the adjoining ends. Traditionally, the adjoining faces were coated with mixed white lead and grease, then held together with copper rivets. It was important to not have the plank end as thin as a feather edge and to have the outboard thin edge at the after end of the joint. In later times, after adhesives had been developed by the aircraft industry, the joint might be made with resin glue and no rivets. In heavier carvel work, the joint would be a butt, riveted to a butt strap. Even large clinker vessels had scarfed strakes as in this form of construction; the strakes contribute a significant proportion of the structural strength of the boat as well as keeping it water-tight.
Assembling the strakes
Two methods used to plank a wooden hull are: carvel in which the edges of the strakes butt against each other, using an internal frame structure to maintain the boat's shape and clinker in which the adjoining strakes are held together on an overlap. Their varying widths and angles of overlap determine the hull's shape.
In the former form of construction, one more traditional in the Mediterranean than in north Europe produces a relatively smooth hull surface but needs caulking to make it watertight and it is relatively heavy (due to the mass of the required internal framing). Carvel boats are planked up onto pre-erected frames which become part of the boat.
The second method is clinker. It is traditional in the north and produced relatively light but strong boats. Normally, the boats are built from the garboard up so that the upper plank overlaps (aka hems) the lower on the outside. That overlap is known as the land and it is held together by copper rivets. In the twentieth century, the boat may have been built of plywood and the strakes glued together without clenched nails. Medieval boats are more likely to have been riveted with iron nails. To rivet the lands, the planks in the two adjoining strakes are pierced, a nail inserted from the outside and a rove or rove punched over the inside end of the nail. The latter is then cut off a little proud of the rove. The nail is then clenched over the rove.
When the shell of the boat is complete, the strakes are stiffened by the insertion of steam-bent timbers. These too, are riveted to the planking through the lands. The timbers, which are sometimes miscalled ribs, spread the load on the strakes and tie them together reducing the tendency of the relatively thin strake to split. With glued ply clinker construction, the timbers are unnecessary.
At the hood-ends of the strakes, where they approach the stem, they are let into each other with geralds (aka chases or gains). In these, the land of the lower strake is tapered to a feather edge at the end of the land where it is supported by the rebate formed by the apron. The strakes then meet the stem flush, which is also referred to as being hooded.
Steel ships may be plated as clinker-built vessels but more usually, they were built with strakes alternately in and out. The modern method is to butt-weld the strakes to each other as well as the plates within them, end to end. This leaves a smoother finish and is lighter.
Sources
- ↑ Keegan, John (1989). The Price of Admiralty. New York: Viking. p. 280. ISBN 0-670-81416-4.