Underground mine ventilation
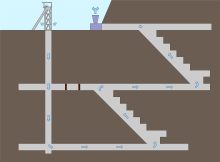
Underground mine ventilation provides a flow of air to the underground workings of a mine of sufficient volume to dilute and remove dust and noxious gases (typically NOx, SO2, methane, CO2 and CO) and to regulate temperature. The source of these gases are equipment that runs on diesel engines, blasting with explosives,[1] and the orebody itself.[2] The largest component of the operating cost for mine ventilation is electricity to power the ventilation fans, which may account for one third of a typical underground mine's entire electrical power cost.[1]
Types of ventilation
Flow-through ventilation is the main ventilation circuit for the mine. Air enters the mine from surface via a shaft, ventilation raise or adit. The air is distributed through the mine via internal ventilation raises and ramps, and flows are controlled by regulators and permanently mounted ventilation fans. An auxiliary ventilation system takes air from the flow-through system and distributes it to the mine workings via temporarily mounted ventilation fans, venturies and disposable fabric or steel ducting. Auxiliary fan and duct systems may be either forcing systems, where fresh air is pushed into mine headings, or exhausting systems that draw out contaminated air.[3]
Ventilation control
Sufficient volume of air is required for proper ventilation. A bulk of electric power is required for driving fans. By installing variable speed control air quantity can be optimized hence the power.[4]
Regulations
The volume (expressed in cubic feet per minute or cubic meters per second) of air required to ventilate an underground mine is determined by mining engineers based on a wide variety of parameters. In most countries minimum requirements are outlined by law, regulation or standards. However, in some developing countries the mandated ventilation requirement may be insufficient, and the mining company may have to increase the ventilation flow, in particular where ventilation may be required to cool the ambient temperature in a deep hot mine, however auto-compression must also be taken into account.[1]
Heating
In temperate climates ventilation air may need to be heated during winter months. This will make the working environment more hospitable for miners, and prevent freezing of workings, in particular water pipes. In Arctic mines where the mining horizon is above the permafrost heating may not take place to prevent melting the permafrost. "Cold mines" such as Raglan Mine and Nanisivik Mine are designed to operate below zero degrees Celsius.[1]
References
- 1 2 3 4 De la Vergne, Jack (2003). Hard Rock Miner's Handbook. Tempe/North Bay: McIntosh Engineering. p. 157. ISBN 978-0-9687006-1-7.
- ↑ MNCU1107A Implement the Ventilation Management Plan - Commonwealth of Australia 2001
- ↑ Darling, Peter (2011). SME Mining Engineering Handbook. United States of America: Society for Mining, Metallurgy, and Exploration, Inc. p. 1583. ISBN 978-0-87335-264-2.
- ↑ Mine Ventilation: Proceedings of the 10th US / North American Mine